Hi all, I'm a mechanical engineer at a research institution building an array of spectrographs. I'm currently designing the coolant assembly and attempting to specify the coolant lines for a minimum of 10 yrs operation with no line maintenance. The other constraints and requirements are listed below. I'm mid career but have very little experience with long-life high-reliability fluid systems, so I am wondering if any of you can suggest a material for the coolant hoses. These CANNOT leak. I've been looking at EPDM, PVC, PTFE, and copper. I like the reliability and low cost of copper lines but we need some flexibility, as these lines attach directly to a detector package, the location of which is very precisely controlled. I cannot induce any significant force on that connection to the detector (less than 1 lbf).
I spent some time on the phone with a Parker-Hannifin applications engineer in their hosing department, but it wasn't very helpful - no confidence or guarantee for any of their lines beyond 1 year. So any tips on hose material selection you all have would be much appreciated!! Thank you all.
Requirements:
Leak free for 10 years.
No maintenance.
Bend radius of < 4 inches
Environment:
Dry air (desert)
10C coolant temperature
20/80 Glycol/Water coolant
Low flow rate (1 gallon/minute)
Low pressure (<50 psi)
0-30 C ambient temperature
Lines are static, do not move (except for ~50 micron travel at mate to detector)
Blue lines indicated needed coolant lines:
I spent some time on the phone with a Parker-Hannifin applications engineer in their hosing department, but it wasn't very helpful - no confidence or guarantee for any of their lines beyond 1 year. So any tips on hose material selection you all have would be much appreciated!! Thank you all.
Requirements:
Leak free for 10 years.
No maintenance.
Bend radius of < 4 inches
Environment:
Dry air (desert)
10C coolant temperature
20/80 Glycol/Water coolant
Low flow rate (1 gallon/minute)
Low pressure (<50 psi)
0-30 C ambient temperature
Lines are static, do not move (except for ~50 micron travel at mate to detector)
Blue lines indicated needed coolant lines:
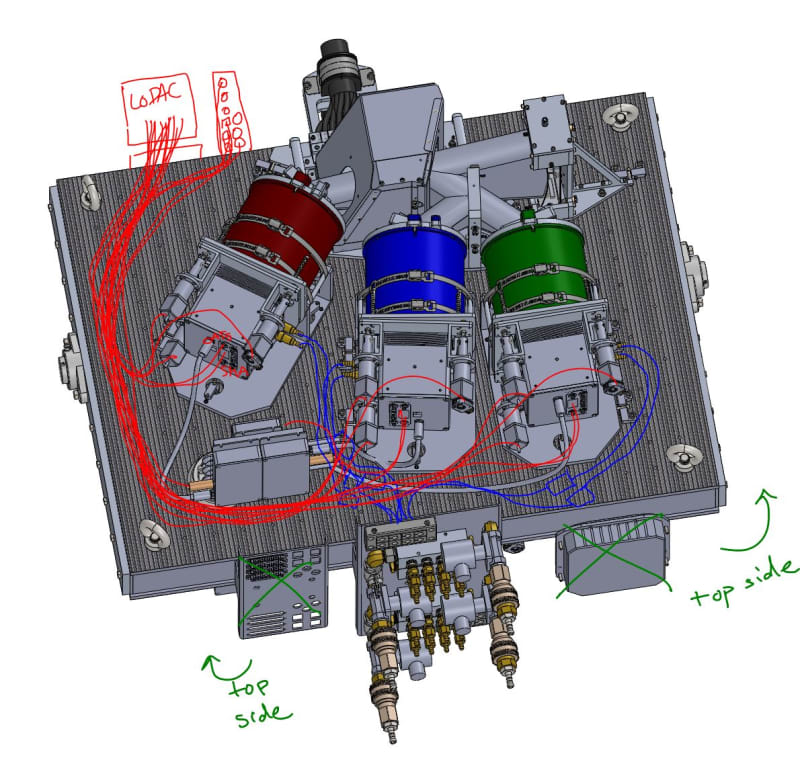