Pavan Kumar
Chemical
- Aug 27, 2019
- 397
Hi All,
I am trying to calculate the pressure drop across the Spray Pipe system for our Cooling Tower cell. We have two cells namely the South and the North Cell. The intention is to rate the existing Cooling Tower circulation Pump for higher flow rate. The pump is supposed to flow 4176 US gpm. I have arbitrarily assumed that the South Cell is getting 2000 gpm while the North gets 2176 gpm. I will get the correct flow rate after I finish my total pressure drop calculations.
Each of the cell has Spray Pipe distribution that sprays hot return cooling water at 32 Deg C on the fill. In-order to size/rate the pump I need to calculate the pressure drop in each of the cell. The pressure drop in each cell is the total of the pressure drops in each of the spray pipe branches.
The calculation spreadsheet based on Perry's 9th Edn Section 6-31 is attached with this thread.
I have calculated the pressure drop in the spray hole= DPo = 4.2 psi
Assuming the spray pipe branches get equal flow, the flow rate in each SPray pipe brnach = 2000 / 6 = 333.33 gpm
Using the flow rate, I calculated the pressure drop across each hole as DPo= 4.2 psi.
There are 3 holes in each spray pipe branch. The total pressure drop of all the holes = 4.2*3 = 12.6 psi.
Per Perry Section 6-31, the pressure variation over the length of the perforated pipe = 1/10th of the pressure drop in the holes
So the pressure drop in the spray pipe branch = (1/10)*4.2*3 = 1.26 psi.
Since two branch start at the same point on the header. The pressure at the center junction point is saame.
so P1 = 1.26 psig, P2 = 1.26 psig, P3= 1.26 psig.
The total pressure at the cell inlet, Po = P1+P2+P3 = 1.26*3 = 3.78 psig.
So each pressure drop P1 = 1/10(4.2*3)=1.26 psi
So the total pressure P0 =(1.26+1.26+1.26)=3.78 psi.
I want to make sure that is analysis is correct.
Thanks and Regards,
Pavan Kumar
I am trying to calculate the pressure drop across the Spray Pipe system for our Cooling Tower cell. We have two cells namely the South and the North Cell. The intention is to rate the existing Cooling Tower circulation Pump for higher flow rate. The pump is supposed to flow 4176 US gpm. I have arbitrarily assumed that the South Cell is getting 2000 gpm while the North gets 2176 gpm. I will get the correct flow rate after I finish my total pressure drop calculations.
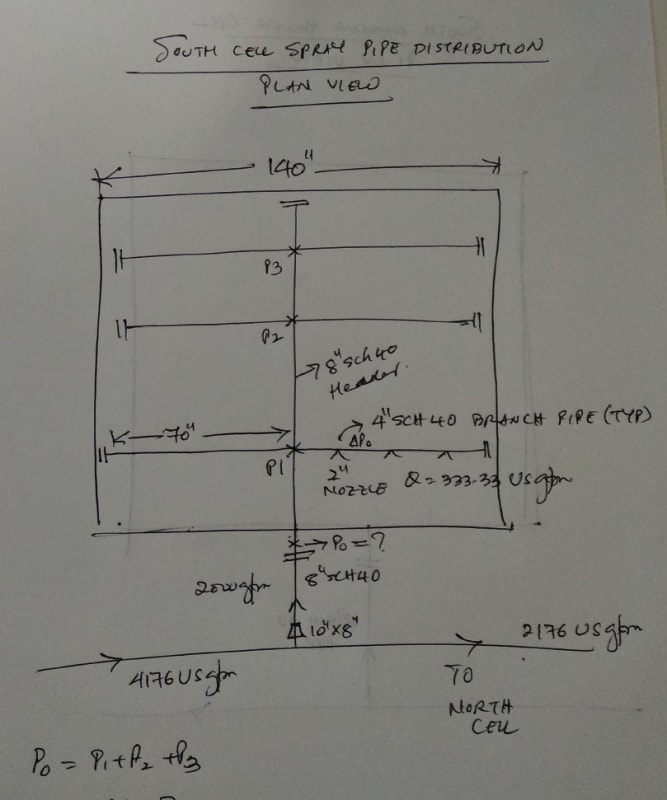
Each of the cell has Spray Pipe distribution that sprays hot return cooling water at 32 Deg C on the fill. In-order to size/rate the pump I need to calculate the pressure drop in each of the cell. The pressure drop in each cell is the total of the pressure drops in each of the spray pipe branches.
The calculation spreadsheet based on Perry's 9th Edn Section 6-31 is attached with this thread.
I have calculated the pressure drop in the spray hole= DPo = 4.2 psi
Assuming the spray pipe branches get equal flow, the flow rate in each SPray pipe brnach = 2000 / 6 = 333.33 gpm
Using the flow rate, I calculated the pressure drop across each hole as DPo= 4.2 psi.
There are 3 holes in each spray pipe branch. The total pressure drop of all the holes = 4.2*3 = 12.6 psi.
Per Perry Section 6-31, the pressure variation over the length of the perforated pipe = 1/10th of the pressure drop in the holes
So the pressure drop in the spray pipe branch = (1/10)*4.2*3 = 1.26 psi.
Since two branch start at the same point on the header. The pressure at the center junction point is saame.
so P1 = 1.26 psig, P2 = 1.26 psig, P3= 1.26 psig.
The total pressure at the cell inlet, Po = P1+P2+P3 = 1.26*3 = 3.78 psig.
So each pressure drop P1 = 1/10(4.2*3)=1.26 psi
So the total pressure P0 =(1.26+1.26+1.26)=3.78 psi.
I want to make sure that is analysis is correct.
Thanks and Regards,
Pavan Kumar