electricpete
Electrical
On our large motors we have (like most) 6 stator RTD’s but we only connect one to our plant computer system. We periodically check to find the hottest one and leave it connected to the computer.
We have frequent problems with erratic indicated winding temperatures creeping up. Often when we investigate the problem is resolved by lifting and relanding the leads (suggesting a problem with corrosion is affecting the connection resistance).
Attached is one of the terminal strips which has found to have more severe corrosion than most. Certainly the screw heads are severely corroded on this one. I'm not sure what else is corroded. I'm reasonably sure we have the same problem (winding temperature creeping up and solved by lifting/landing leads) on other motor terminal strips that don’t look nearly as bad as this one.
For this particular terminal strip, we have a motor refurbishment coming up shortly, I’m going to replace the terminal strip and replace the RTD lugs (with ring lugs).
My question: Are there any practices to help prevent the corrosion (something that could be done during our periodic check).
Is there some type of compound that could be applied before or after tightening the terminations to help improve the resistance of the connection to being disrupted by corrosion?
PS. I'm not looking to install a heater (too much effort). I might be open to changing terminal screws or strips if there is a better choice someone can recommend.
=====================================
(2B)+(2B)' ?
We have frequent problems with erratic indicated winding temperatures creeping up. Often when we investigate the problem is resolved by lifting and relanding the leads (suggesting a problem with corrosion is affecting the connection resistance).
Attached is one of the terminal strips which has found to have more severe corrosion than most. Certainly the screw heads are severely corroded on this one. I'm not sure what else is corroded. I'm reasonably sure we have the same problem (winding temperature creeping up and solved by lifting/landing leads) on other motor terminal strips that don’t look nearly as bad as this one.
For this particular terminal strip, we have a motor refurbishment coming up shortly, I’m going to replace the terminal strip and replace the RTD lugs (with ring lugs).
My question: Are there any practices to help prevent the corrosion (something that could be done during our periodic check).
Is there some type of compound that could be applied before or after tightening the terminations to help improve the resistance of the connection to being disrupted by corrosion?
PS. I'm not looking to install a heater (too much effort). I might be open to changing terminal screws or strips if there is a better choice someone can recommend.
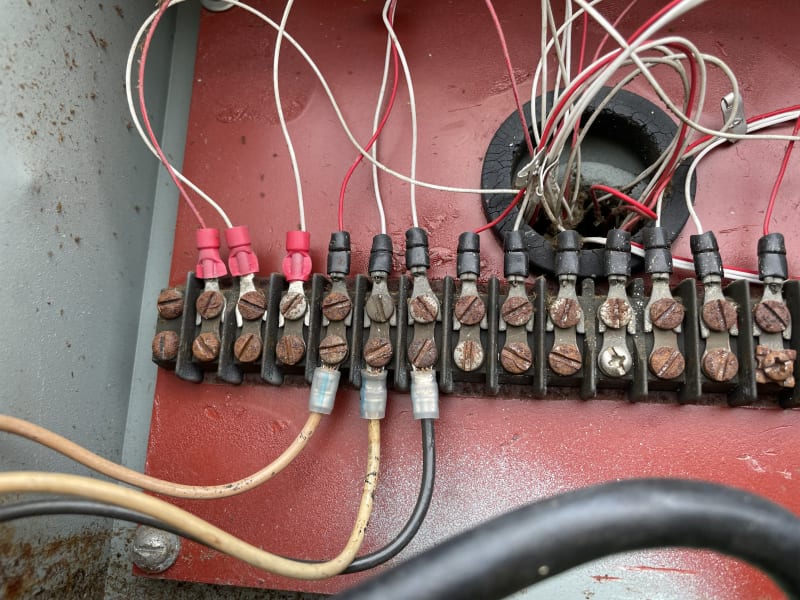
=====================================
(2B)+(2B)' ?