We are a fabrication company that specializes in waste water treatment plants. We recently completed a project in Phoenix, AZ where we replaced two drum screens at one of the largest waste water facilities in the country. These drum screens are not supposed to be on the sanitary (sewage) side, but rather on the run-off (storm drain) side.
The replacement screens and covers were set in place November of last year. In March of this year, they were tested in dry-bed conditions (the water ways were empty) but we did run the clean out spray nozzles for quite a while. The plant was also charged with running the screens and nozzles weekly until full operation is in play (October of this year). These units are exposed to the elements and are not contained within any facility.
We were able to save the original interior drum skeleton. This drum is made of carbon steel and is coated with Dura-Plate (Sherwin Williams) and was Holiday tested for proper coating thickness and coverage. We did have to add new 304 stainless screens and 304 stainless steel screen plates to the drum. We used 316 stainless hardware to connect everything.
We also built new 304 stainless steel covers, along with all 304 stainless piping when the units were installed.
The plant has now tested the units with the water ways full as if in actiive opoeratioon (remember, these are not suposed to go on line until October of this year). I have no idea how long they tested or how many times they have tested, but they have sent us these pictures:
This first picture is the outside face of the actual drum that sits inside the cover. Remember, the drum skeleton is carbon steel coated with Durua-Plate and the outer plates and screen are 304 stainless while the hardware is 316 stainless. Notice that the screen material does not look to have this discoloration. What is causing this and the stuff that looks like somebody sprayed something on the outer cover?
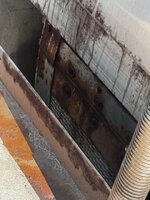
We have a theory and I will disclose that after we get some comments related to what this may be.
This next picture is of a 304 braided stainless steel flexible hose. This will be changed out to hard pipe (against my urge to leave as is):
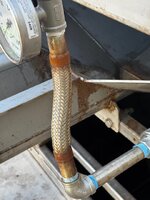
Note there is more staining on the catch trough in the background.
These next two pictures are the welds on the 304 stainless piping: (ignore the fact that the one flange is missing nuts. I have already addressed this)
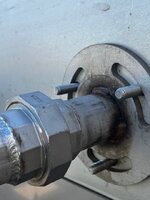
The contractor in charge of this project is looking for answers before they turn it back over to the city. I am hoping that someone can help me analyze this to see if there is anything that can be done to have prevented this (using the materials listed) and if there is anything that can be done to prevent it happening any further.
Again, when we tested the system (early March), these did not look like this. A month later and this is what we have. So, we feel pretty sure that this has something to do with the water they are running in and something to do with the H2S gasses these are subjected to. We also feel, short of additional coatings or alternate materials, that there is nothing we could have to done to prevent the corrosion on the screen parts (the welds could just be where the welds weren't cleaned or passivated).
Any input is greatly appreciated.
The replacement screens and covers were set in place November of last year. In March of this year, they were tested in dry-bed conditions (the water ways were empty) but we did run the clean out spray nozzles for quite a while. The plant was also charged with running the screens and nozzles weekly until full operation is in play (October of this year). These units are exposed to the elements and are not contained within any facility.
We were able to save the original interior drum skeleton. This drum is made of carbon steel and is coated with Dura-Plate (Sherwin Williams) and was Holiday tested for proper coating thickness and coverage. We did have to add new 304 stainless screens and 304 stainless steel screen plates to the drum. We used 316 stainless hardware to connect everything.
We also built new 304 stainless steel covers, along with all 304 stainless piping when the units were installed.
The plant has now tested the units with the water ways full as if in actiive opoeratioon (remember, these are not suposed to go on line until October of this year). I have no idea how long they tested or how many times they have tested, but they have sent us these pictures:
This first picture is the outside face of the actual drum that sits inside the cover. Remember, the drum skeleton is carbon steel coated with Durua-Plate and the outer plates and screen are 304 stainless while the hardware is 316 stainless. Notice that the screen material does not look to have this discoloration. What is causing this and the stuff that looks like somebody sprayed something on the outer cover?
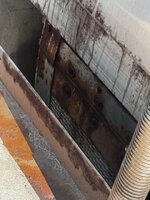
We have a theory and I will disclose that after we get some comments related to what this may be.
This next picture is of a 304 braided stainless steel flexible hose. This will be changed out to hard pipe (against my urge to leave as is):
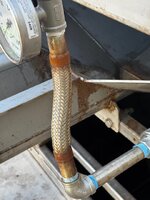
Note there is more staining on the catch trough in the background.
These next two pictures are the welds on the 304 stainless piping: (ignore the fact that the one flange is missing nuts. I have already addressed this)
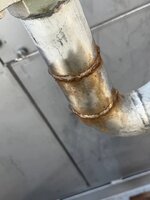
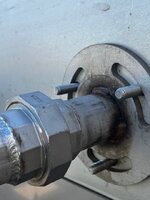
The contractor in charge of this project is looking for answers before they turn it back over to the city. I am hoping that someone can help me analyze this to see if there is anything that can be done to have prevented this (using the materials listed) and if there is anything that can be done to prevent it happening any further.
Again, when we tested the system (early March), these did not look like this. A month later and this is what we have. So, we feel pretty sure that this has something to do with the water they are running in and something to do with the H2S gasses these are subjected to. We also feel, short of additional coatings or alternate materials, that there is nothing we could have to done to prevent the corrosion on the screen parts (the welds could just be where the welds weren't cleaned or passivated).
Any input is greatly appreciated.