Mononcue
Mechanical
- Aug 7, 2008
- 5
I have some parts wire edm cut from a round blank of 440C. The material is hardened to 52-56 HRC per AMS 2759/5 type 3 with sub zero cooling. The certs say it is 54-55 HRC. During the edm process the tips of my part tend to crack. This has only occurred twice out of many parts, but since it happens on the final process it is expensive as it scraps the whole blank. Last time this happened I had the remaining blanks drawn back a little and had no further problem. But now I have had the problem reoccur and I’m looking for ideas. The cracking only happens on a sharp edge near the center of the blank. Suggestions as to what may be the cause are welcomed as well as cures.
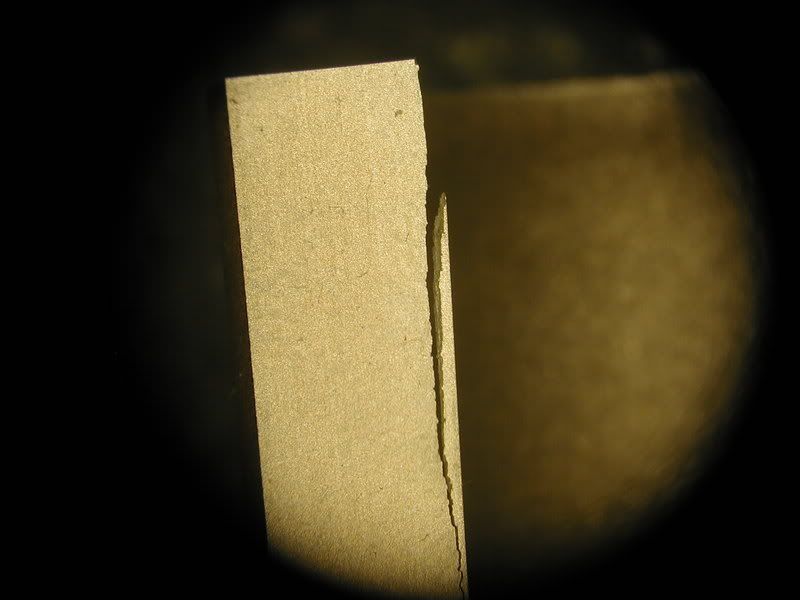
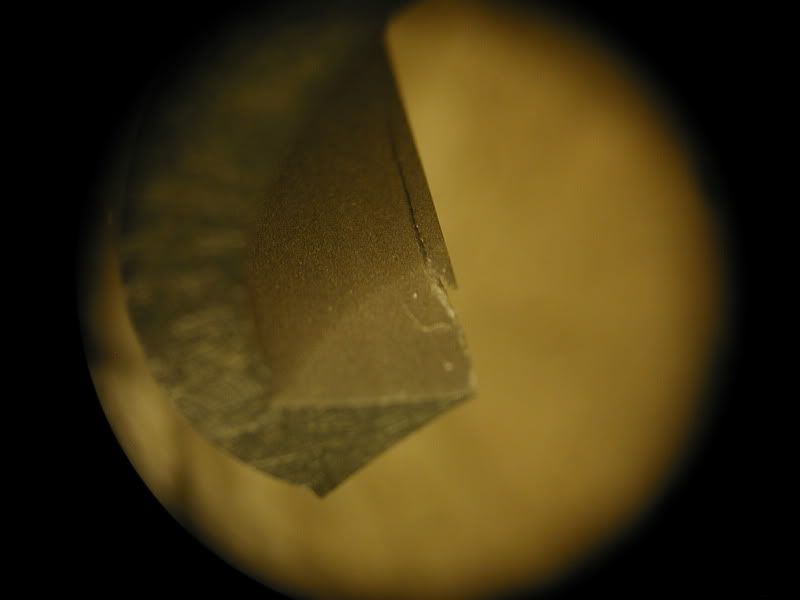
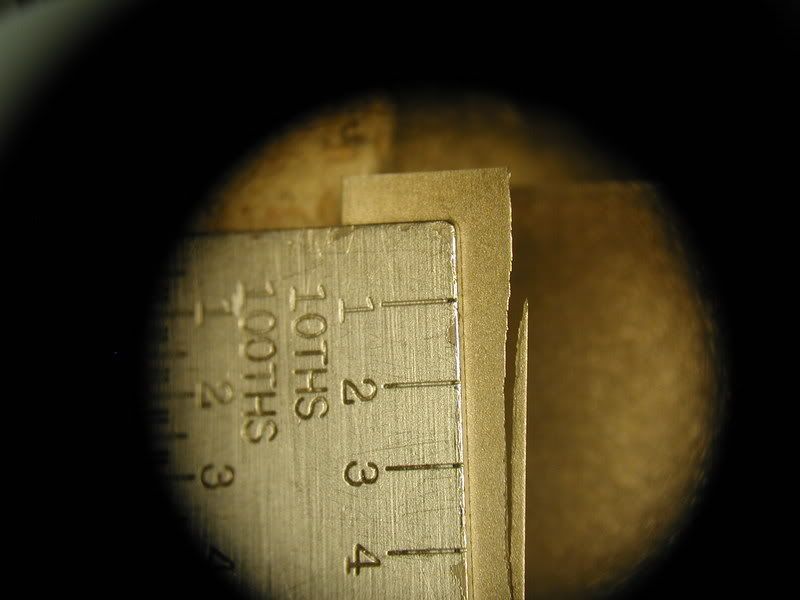
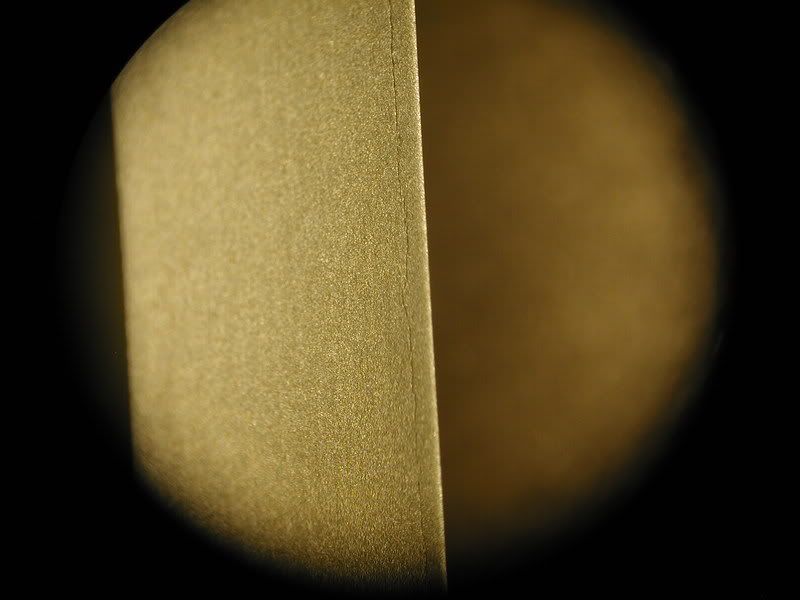