VaidehiChennubhotla
Mechanical
Hi,
A Crushable foam material model was used for compression test on a 50x50x50 mm block. The compression test data (FS curve) was overlaid on the CAE data. The test data seems a little softer as it we go down the curve, compared to what I am getting in the analysis. I have played around with parameters like K, Kt and poisson ratio and adjusted the test data to have more spacing. It didnt help. Then I tried using a single element mesh for the foam block, it made the curve stiffer. When I removed the indenter and removed global stabilize from my model it became softer. Either way, I am having difficulty to match the CAE data to Test data. What more can be done to the Crushable foam material card, to make it match with test data ?
Any help would be greatly appreciated.
Here is a picture showing test vs CAE data.
Thanks,
Vaidehi
A Crushable foam material model was used for compression test on a 50x50x50 mm block. The compression test data (FS curve) was overlaid on the CAE data. The test data seems a little softer as it we go down the curve, compared to what I am getting in the analysis. I have played around with parameters like K, Kt and poisson ratio and adjusted the test data to have more spacing. It didnt help. Then I tried using a single element mesh for the foam block, it made the curve stiffer. When I removed the indenter and removed global stabilize from my model it became softer. Either way, I am having difficulty to match the CAE data to Test data. What more can be done to the Crushable foam material card, to make it match with test data ?
Any help would be greatly appreciated.
Here is a picture showing test vs CAE data.
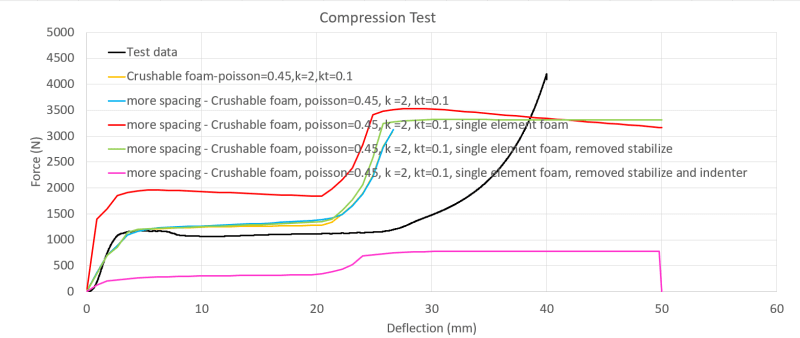
Thanks,
Vaidehi