drennon236
Civil/Environmental
I have 2 steel cylindrical parts, and in the middle is a cylindrical part (concrete - grout). The concrete part is supposed to stop any movement between the parts simply through friction. Below the interaction properties are shown:
Interaction between concrete (grout) and upper steel part and lower steel part:
Interaction properties:
CSTATUS:
Pretty much all nodes seem to be open, I tried to fix this by setting sliding formulation to "small sliding" and uniform value across slave surface to zero. Shouldn't all nodes be closed? Or atleast sliding? Is there something I am misunderstanding, and how can I fix this? I know a finer mesh helps with this, but the improvement was minimal when I tried.
Interaction between concrete (grout) and upper steel part and lower steel part:
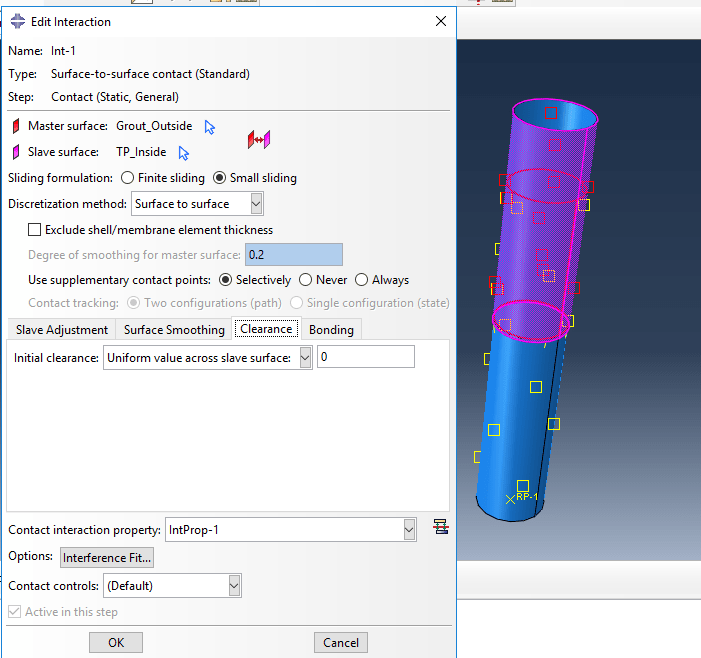
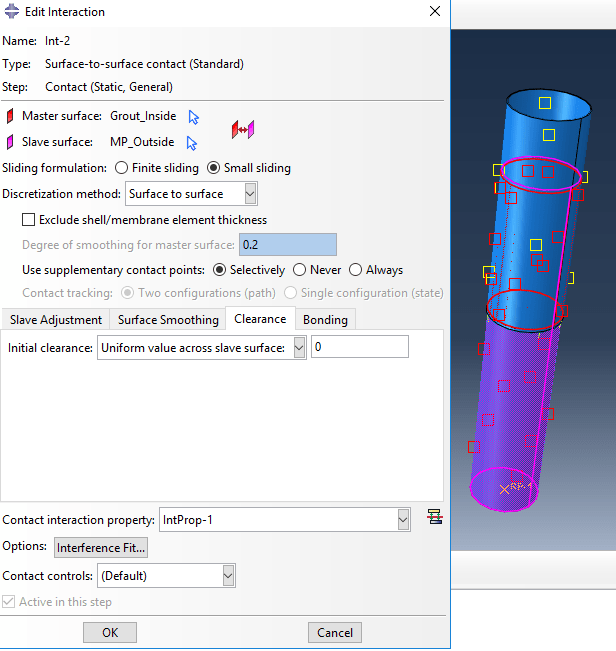
Interaction properties:
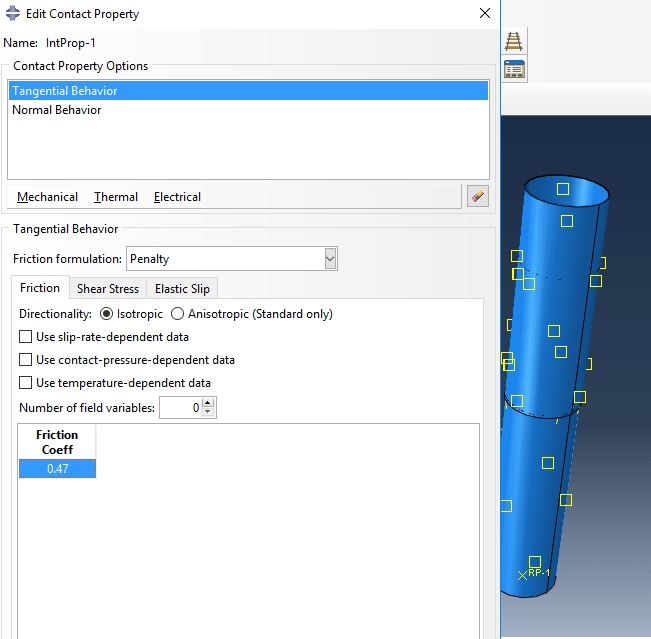
CSTATUS:

Pretty much all nodes seem to be open, I tried to fix this by setting sliding formulation to "small sliding" and uniform value across slave surface to zero. Shouldn't all nodes be closed? Or atleast sliding? Is there something I am misunderstanding, and how can I fix this? I know a finer mesh helps with this, but the improvement was minimal when I tried.