Polishmafiaboss
Industrial
- Jun 4, 2019
- 5
Running an Amada LC-1212-A3 (2KW Fanuc Laser / Fanuc 160iL control). We've had it running now about 9 months mostly cutting 26ga to 13ga stainless and galvanized. We are working on a project for our sister company to cut some parts out of .375CRS. I'm not having much luck with part of it. The tricky part of this is that the part has teeth that we need to make as perfect as we can get them. So far I can either get good edges and crappy teeth or crappy edges and pretty decent teeth. I think I'm to the fine tuning point, but my brain is now mush from trying to figure this out. I'm attaching cut condition tables/edge control table pics and a couple of the best part I've gotten so far. A few notes: (1) we're using O2 (shop air doesn't seem to be a viable option for this part). (2) The parts in the photo were cut using E3 with a M103 pierce that was done 3/8" away from the part with a lead-in. The pierce is acceptable, altho it could be close enough to the part that it is causing thermal spots at that end. (Not sure about that just yet.)
Edit
ics didn't load correctly, I think I got that fixed. Other item to note: In our Cut Condition table, there was NOT an entry for CRS .375. Only went up to .120. So I've been using the HRS .375 condition, which is likely part of my problem.
Any suggestions or observations of the settings would be greatly appreciated. I'm about at the end of O2 bottle #1 and would rather not waste much more trying to dial this in. Once we get it to cut "acceptably", we need to run about 16K of these as quickly as we can!!
Thanks guys!!![[ponder] [ponder] [ponder]](/data/assets/smilies/ponder.gif)
Edit
Any suggestions or observations of the settings would be greatly appreciated. I'm about at the end of O2 bottle #1 and would rather not waste much more trying to dial this in. Once we get it to cut "acceptably", we need to run about 16K of these as quickly as we can!!
Thanks guys!!
![[ponder] [ponder] [ponder]](/data/assets/smilies/ponder.gif)
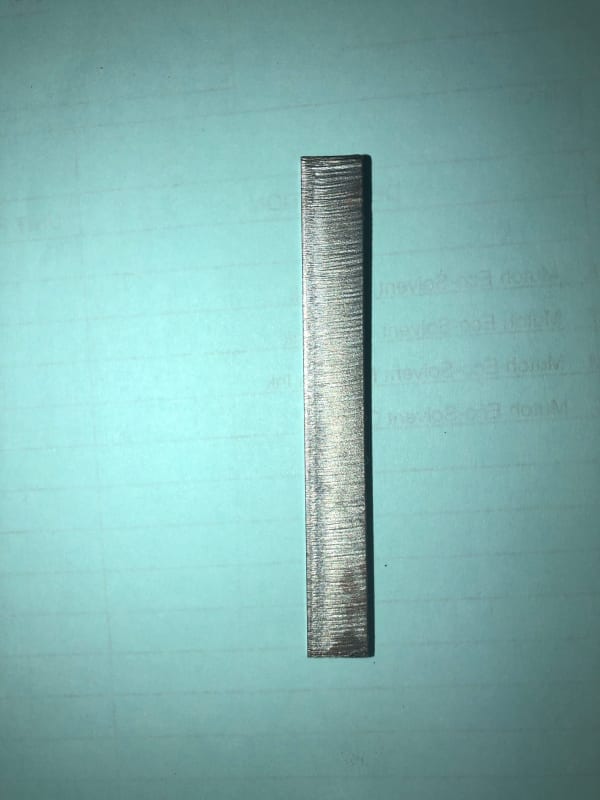
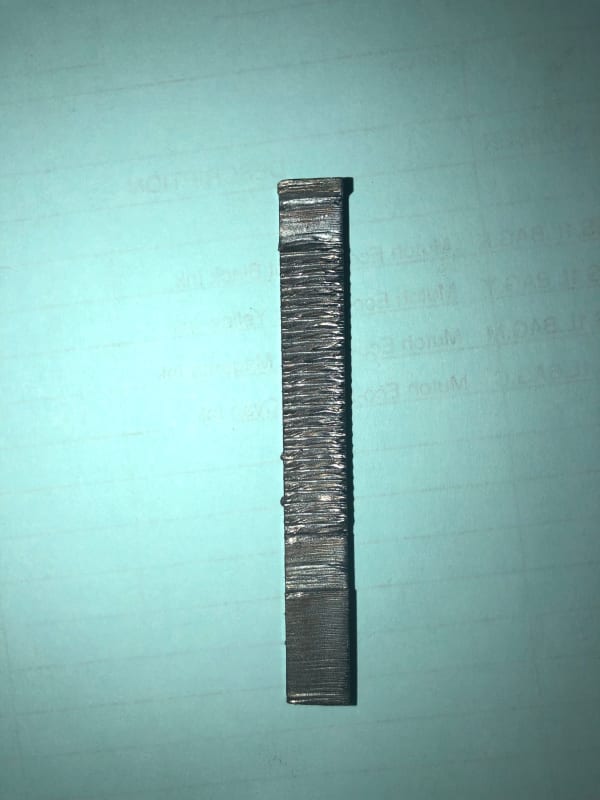
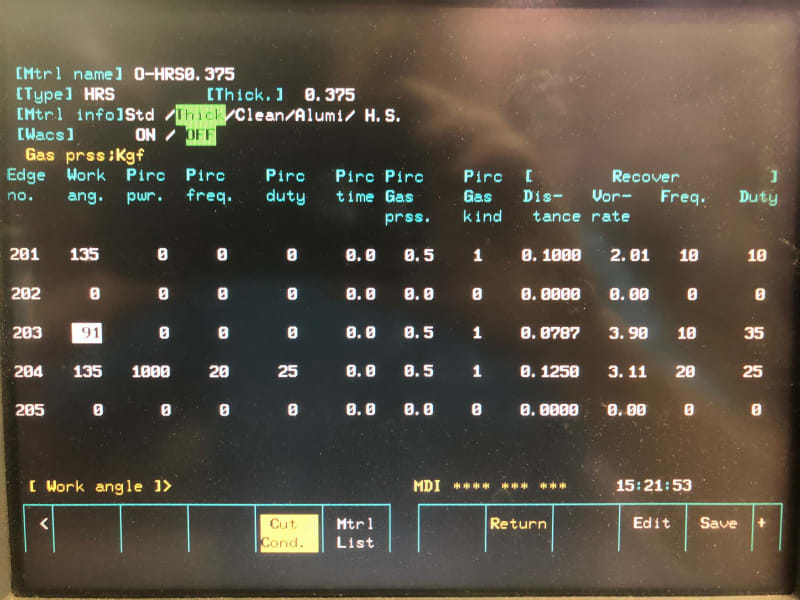
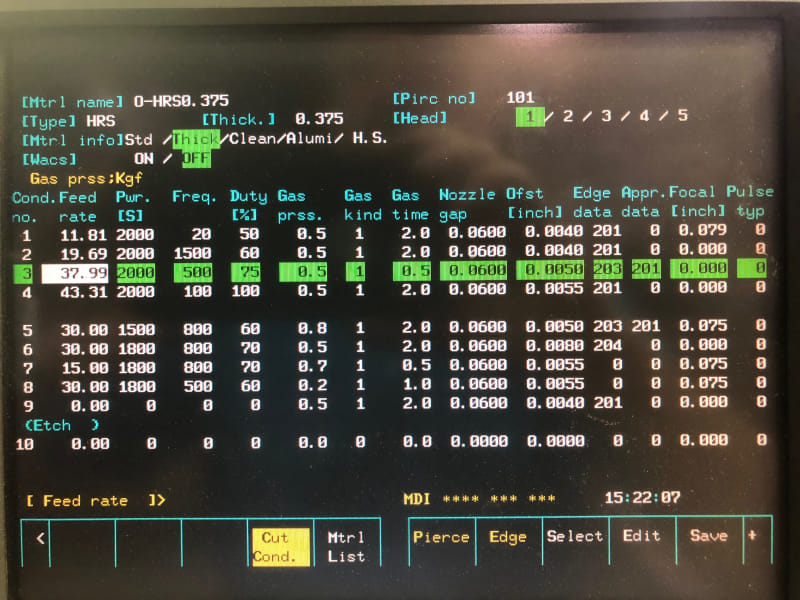