robsalv
Mechanical
- Aug 8, 2002
- 311
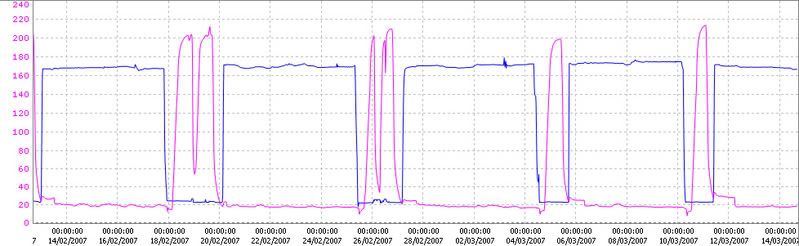
This is a typical one month trend of one of our catalyst filled drier vessesls.
I need to assess just how much credence I give to thermal and cyclic loading degradation concerns for this vessel.
The pink line is operating temperature - it varies between ~20DegC (normal operation) to ~200degC (regen cycle) with a temperature rate change of 25 - 30 DegC/hr. The blue line is operating pressure, which varies between ~450kPa (regen cycle) to ~3150kPa (normal operation).
The vessel is approximately 1.8m diam x 5.6m x ~36mm thick, 100% radiographed and stress relieved, with a DT=343 DegC & DP = 3999kPa. Material is A515 CS and is now approaching 37yrs old.
I've yet to have a good look in ASME VIII, but I've had a look through some other resources and this vessel seems to fall outside of the cyclic loading requirements, because it doesn't go through full cycles in either pressure or temperature, but I'm still not convinced that this vessel doesn't need to be treated with cyclic kid gloves. For the record, the original vessel design doesn't have any specific cyclic design aspects built in.
One resource recommended a cyclic design review for a cyclic deltaT of >93degC, and also recommended using a low temperature rate change to alleviate concerns - but it didn't give any indication for what that rate should be.
API579's cyclic thermal considerations were a bit more convoluted - but I suspect that at the heating rate mentioned above, the whole vessel pretty much warms up gradually and almost homogeneously so thermal issues might not come into play.
Any helpful hints, thoughts or guidance would be greatly appreciated.
Thanks in advance.