Amr Mohamed
Mechanical
Dears;
I am designing a pressure vessel as per ASME Div.1 Edition 2019, the client requested that the vessel has a rectangular nozzle with filleted corners, and a flat door to close it against a rubber air tight gasket, during the entire vessel design phase I haven't faced any problems except when I started designing the head and that hugely large, weirdly shaped opening, a detailed analysis of the door, door frame and adjacent shell is required which after further research, I found out that using design by analysis rules of div 2 (as indicated by Mandatory Appendix 46). I created a 3d Model for the head and the doorway to perform the FEA on. According to div 2 rules the stress classification line should be perpendicular to both the inner and outer surfaces of the head (aligned radially) however, the line starting at the toe of the inner fillet weld joining the nozzle and the head and ending at the outer weld's toe is not perpendicular to the two surfaces, as both welds have the same size; and according to ASME PTB 3 2013 there should be a stress classification line at the toe of the weld. the only way I see is to make them of different (and probably bizarre) sizes so the points create a radial Stress classification line which I can use to find linearized stress results. Am I over thinking this? is it ok if the stress classification line is not exactly radial? is there anything I am missing? I am actually in need of any help to find out whether I have been doing right with this project or not.
Thanks for your time to read this, any help whether by a reference, an old thread or an opinion would be very appreciated.
I am designing a pressure vessel as per ASME Div.1 Edition 2019, the client requested that the vessel has a rectangular nozzle with filleted corners, and a flat door to close it against a rubber air tight gasket, during the entire vessel design phase I haven't faced any problems except when I started designing the head and that hugely large, weirdly shaped opening, a detailed analysis of the door, door frame and adjacent shell is required which after further research, I found out that using design by analysis rules of div 2 (as indicated by Mandatory Appendix 46). I created a 3d Model for the head and the doorway to perform the FEA on. According to div 2 rules the stress classification line should be perpendicular to both the inner and outer surfaces of the head (aligned radially) however, the line starting at the toe of the inner fillet weld joining the nozzle and the head and ending at the outer weld's toe is not perpendicular to the two surfaces, as both welds have the same size; and according to ASME PTB 3 2013 there should be a stress classification line at the toe of the weld. the only way I see is to make them of different (and probably bizarre) sizes so the points create a radial Stress classification line which I can use to find linearized stress results. Am I over thinking this? is it ok if the stress classification line is not exactly radial? is there anything I am missing? I am actually in need of any help to find out whether I have been doing right with this project or not.
Thanks for your time to read this, any help whether by a reference, an old thread or an opinion would be very appreciated.
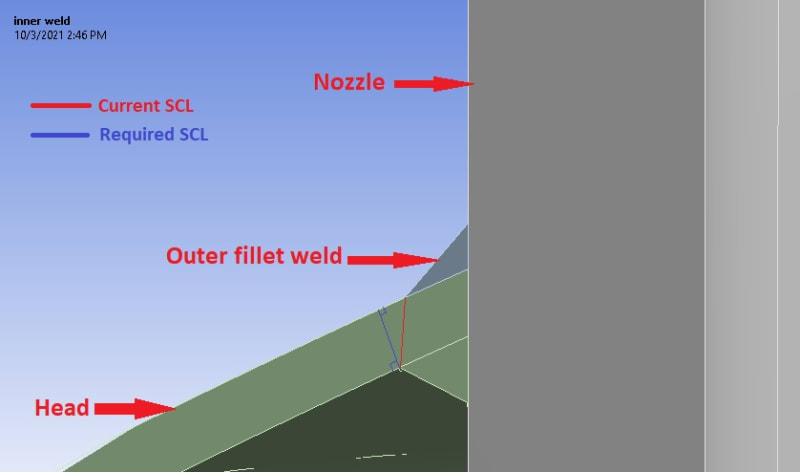