Good morning,
I am in the process of completing a data book for an H2O filter skid for customer and they've asked for allowable load calculations (Forces - axial, circumferential, longitudinal; Moments - axial, circumferential, torsional).
I'm not sure how to get to this as is completely different it seems for the MOC which is Centricast CL-2030 piping with CL-200 adhesive joined to CL Vinyl Ester flanges in size from 1, 1-1/2, 2 and 3 inches.
The picture uploaded is an example of how the FRP piping system along one run is attached to the skid with bolted and padded supports.
See Manufacturer document and lend any advice as appropriate, many thanks.
I am in the process of completing a data book for an H2O filter skid for customer and they've asked for allowable load calculations (Forces - axial, circumferential, longitudinal; Moments - axial, circumferential, torsional).
I'm not sure how to get to this as is completely different it seems for the MOC which is Centricast CL-2030 piping with CL-200 adhesive joined to CL Vinyl Ester flanges in size from 1, 1-1/2, 2 and 3 inches.
The picture uploaded is an example of how the FRP piping system along one run is attached to the skid with bolted and padded supports.
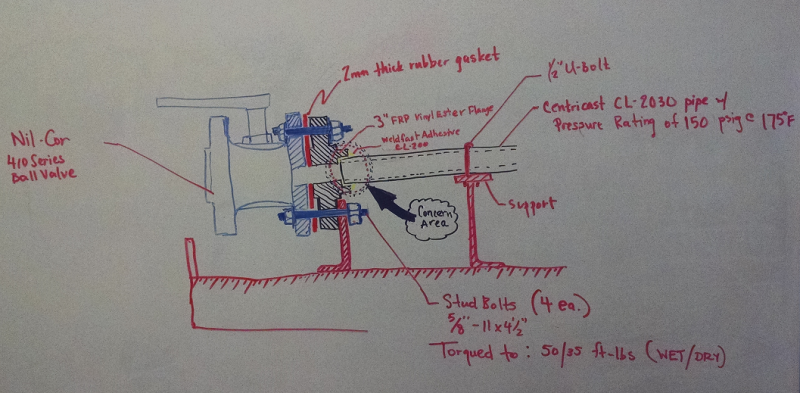
See Manufacturer document and lend any advice as appropriate, many thanks.