MikeOBrien
Mechanical
Hello fellow users,
I am trying to create flat profiles for some swept boxed rails that we use to create frame rails for custom tailored cars. We do not mandrel bent existing box tubing, but cut out all four sections with a CNC plasma and tig weld them together. This allows us to be extreemly creative and produce profiles that are strong and very visually pleasing to the higher market customers we serve. (No wrinkles and smooth transitions)
I have been using sweeps mainly to assure that I have a gaussian surface to use for creating a sheet metal part. I extrude a profile as such:
I then convert it to a sheet metal part so that I can flatten the part to create the templeate we need to cut from our plasma. The problem is that when I do, I cannot seem to avoid the relief cuts that solidworks automatically produces in each sweep:
Here are four pieces assembled for a visual reference:
I have been getting by simply by filling the reliefs with material before I export them to our plasma tech, but this process is time wasted and slows down our fork flow on complex models. (The example I am showing here is very simple)
My main question is this: How can I dissable or get around the automated relief cuts in SolidWorks sheet metal? Is there another process that would be less time consuming and produce the same results. Remember, I don't really care to reassemble the parts bent into an assembly, I simply want to deconstruct a profile into it's flattened profile so we can then cut it out very accurately. This is the end goal:
Thanks for any help or suggestions,
-Mike
Mike O'Brien
Mechanical Engineer
The Roadster Shop,
I am trying to create flat profiles for some swept boxed rails that we use to create frame rails for custom tailored cars. We do not mandrel bent existing box tubing, but cut out all four sections with a CNC plasma and tig weld them together. This allows us to be extreemly creative and produce profiles that are strong and very visually pleasing to the higher market customers we serve. (No wrinkles and smooth transitions)
I have been using sweeps mainly to assure that I have a gaussian surface to use for creating a sheet metal part. I extrude a profile as such:
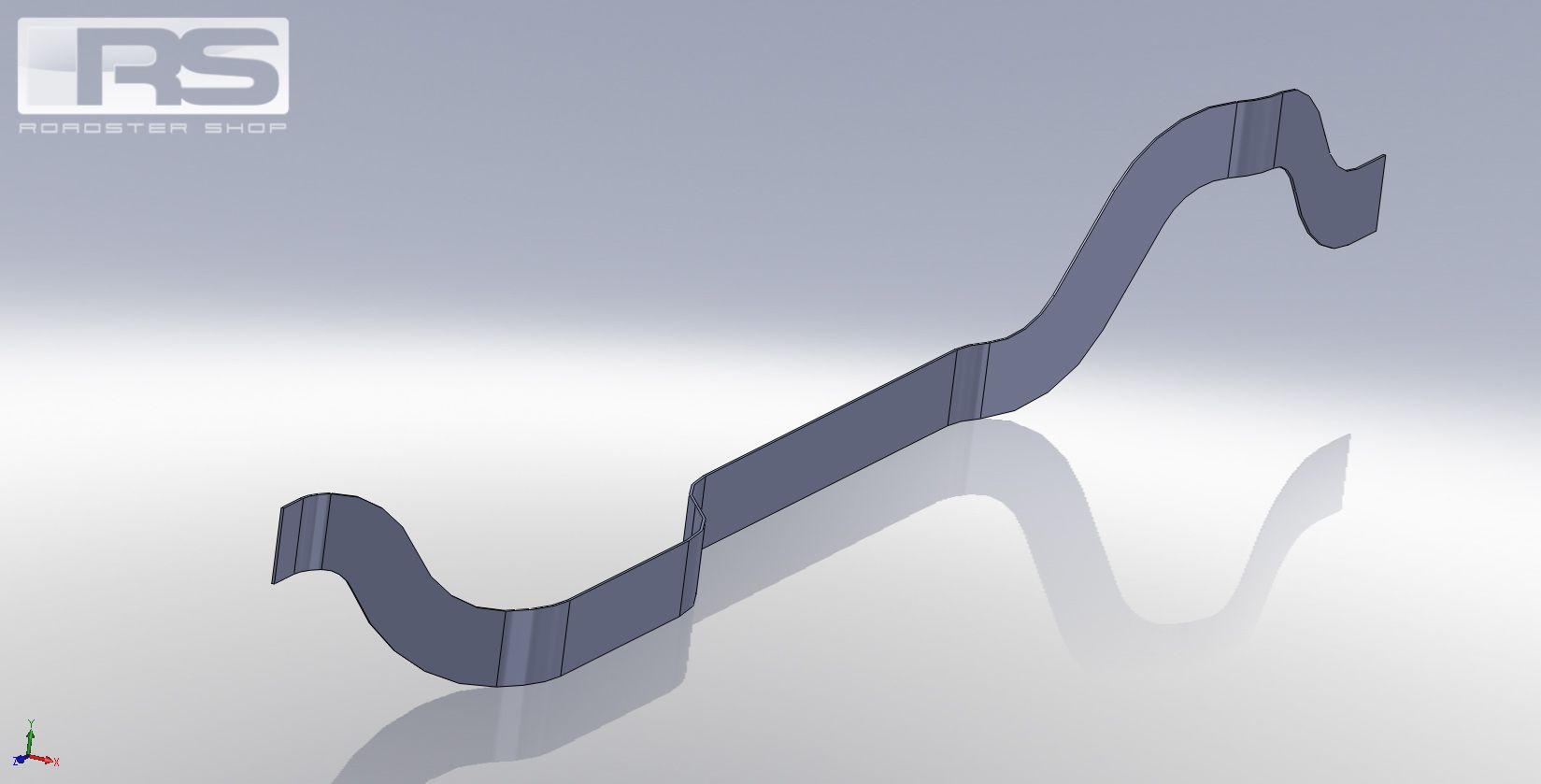
I then convert it to a sheet metal part so that I can flatten the part to create the templeate we need to cut from our plasma. The problem is that when I do, I cannot seem to avoid the relief cuts that solidworks automatically produces in each sweep:
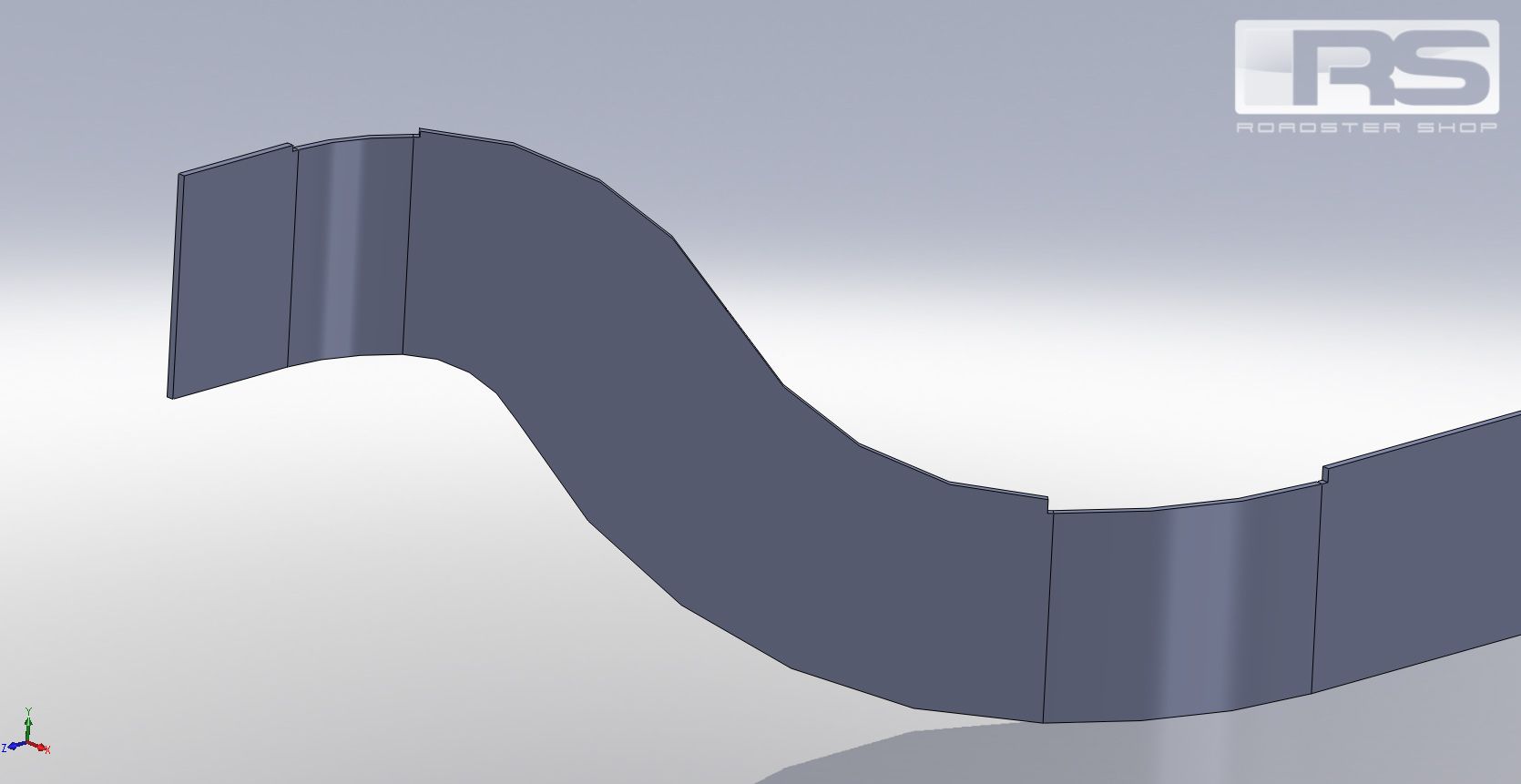
Here are four pieces assembled for a visual reference:
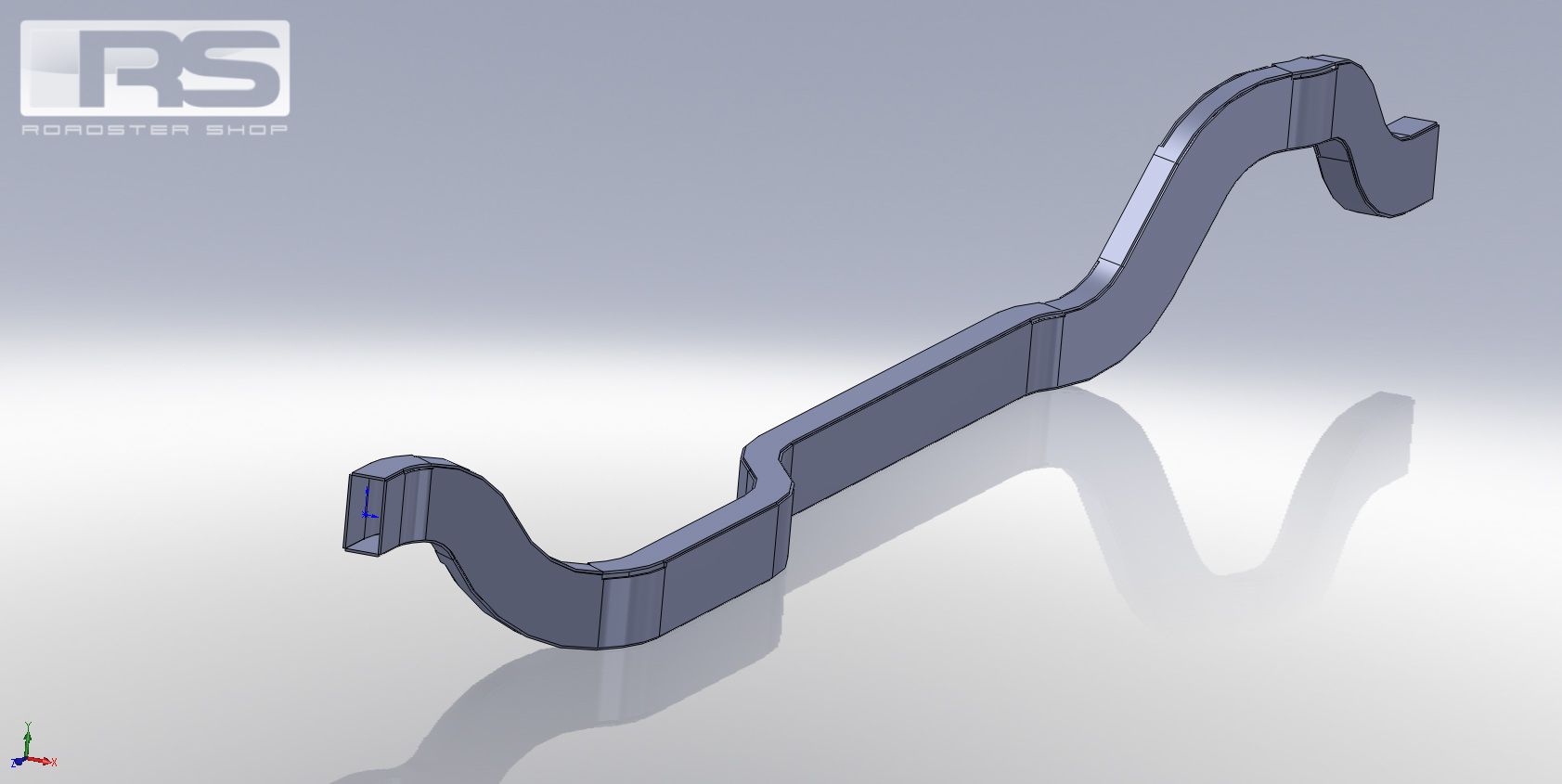
I have been getting by simply by filling the reliefs with material before I export them to our plasma tech, but this process is time wasted and slows down our fork flow on complex models. (The example I am showing here is very simple)
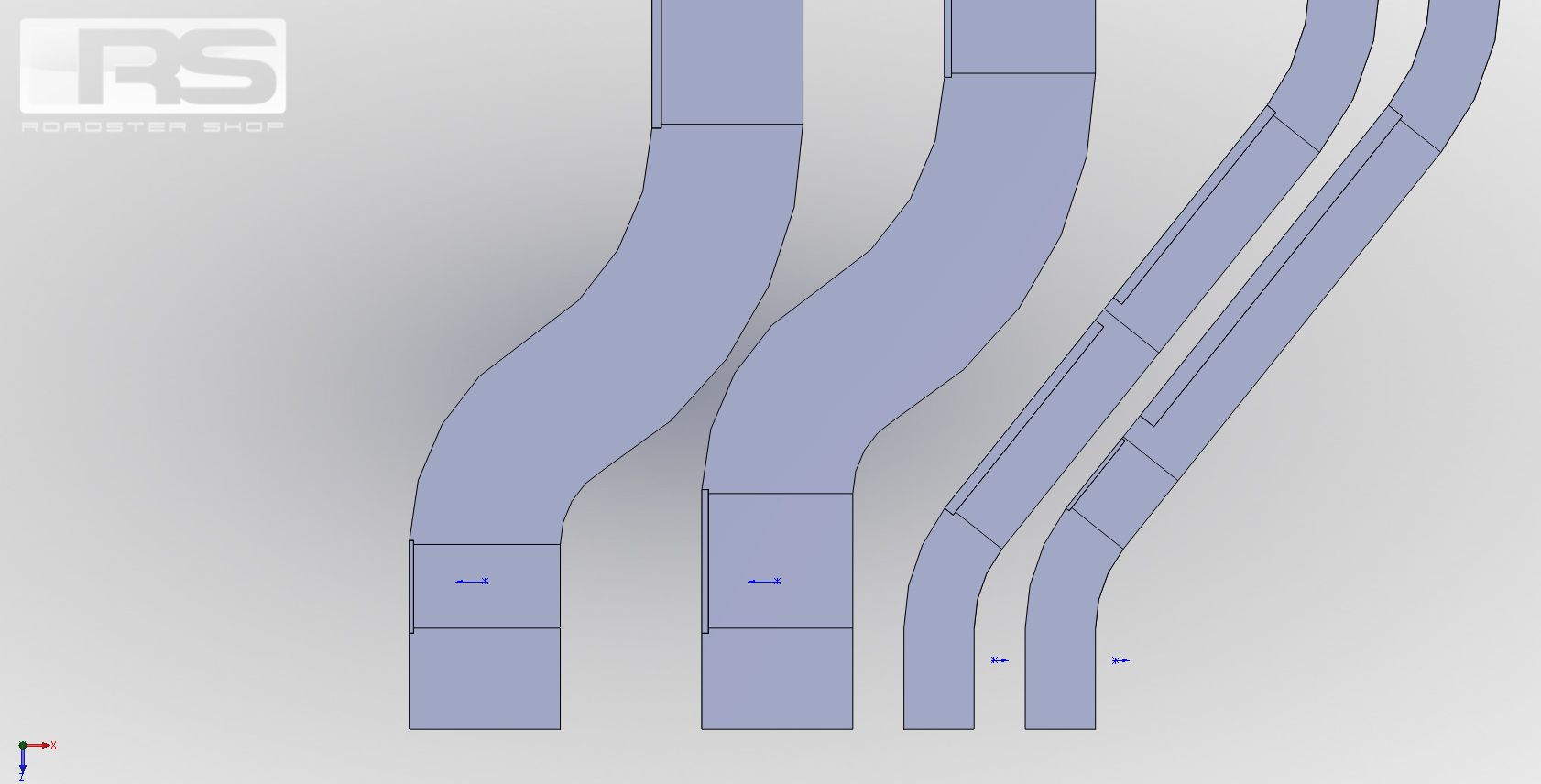
My main question is this: How can I dissable or get around the automated relief cuts in SolidWorks sheet metal? Is there another process that would be less time consuming and produce the same results. Remember, I don't really care to reassemble the parts bent into an assembly, I simply want to deconstruct a profile into it's flattened profile so we can then cut it out very accurately. This is the end goal:
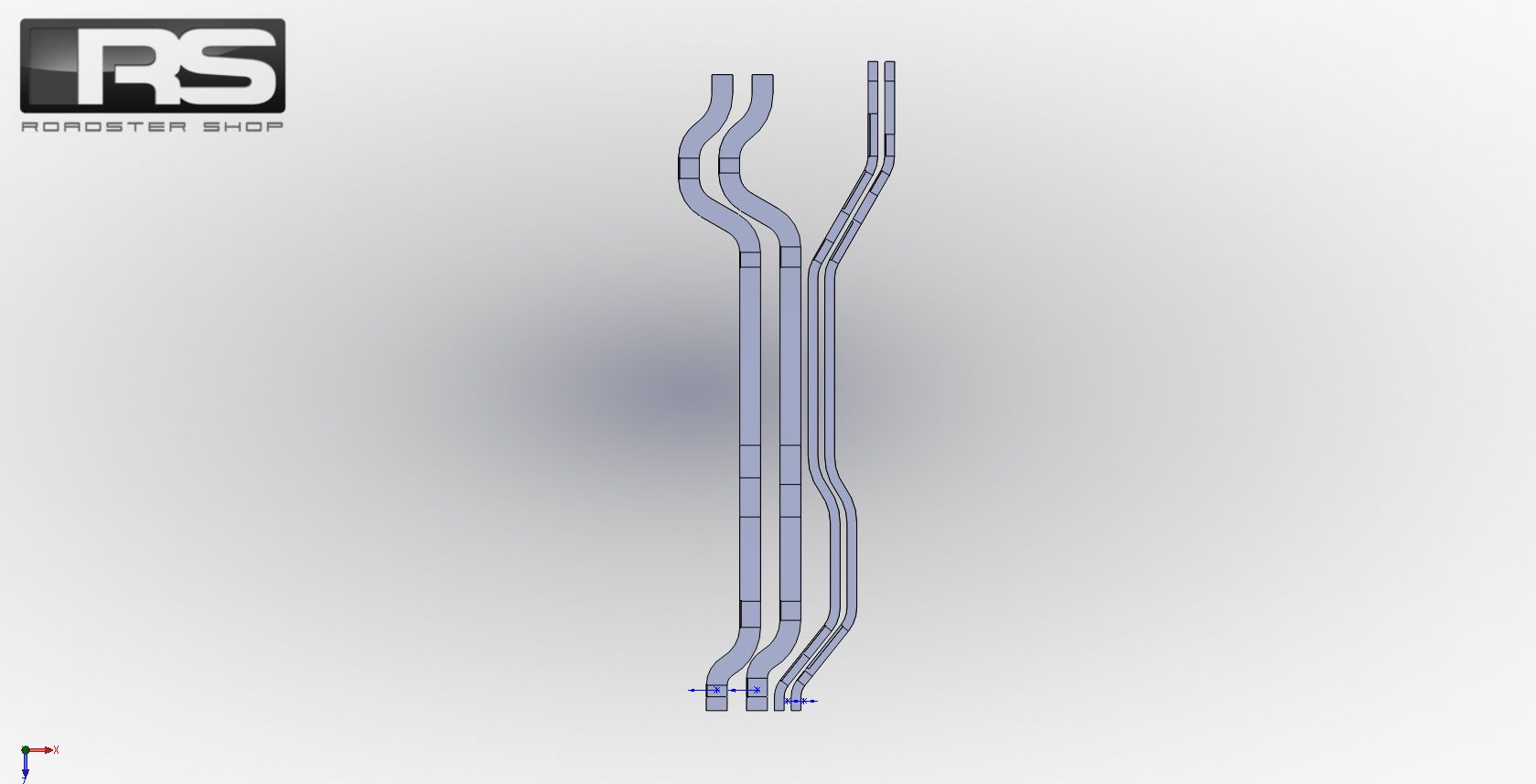
Thanks for any help or suggestions,
-Mike
Mike O'Brien
Mechanical Engineer
The Roadster Shop,