DriveMeNuts
Mechanical
- May 4, 2018
- 447
A pad is welded to the outside of a shell. The pad has external loading applied to it. I am trying to correctly find the membrane and bending stresses in the shell at the edge of the pad.
My understanding is that the purpose of Linearization is to remove the peak stress so that membrane and bending components can be found for each element of the stress tensor. Linearization according to ASME VIII Div 2 Annex 5-A is obviously applicable to the end of the stress classification line where the discontinuity (or pad) is.
However, I am wondering how to handle the stress at the other end of the stress classification line (the inside surface of the vessel). As there is no discontinuity or peak stress, is there a need to use the linearised M+B equivilant stress or can you use the "total" equivilant stress.
I ask because when linearizing in accordance with Div 2 using ANSYS 19.1 with through thickness bending set to Zero the following plot is the result. The blue membrane plus bending line looks good on the left where the discontinuity is. However it results in an equivilant stress that is 20% higher than the total equivilant stress on the right.
There are 3 stress components: Membrane, Bending and Peak. As there is no peak stress on the right, the blue Membrane Plus bending line should be very close to the brown total stress line. Why is the the blue line 20% higher? It looks like a conservative penalty to me.
The following graph is for through thickness bending "not" set to Zero. It appears to produce a poorer quality result on the left but a good result that closely matches the total stress on the right.
My suspicion is that if I was to model the geometry using shell elements, and apply the Div 2 shell element linearization rules then the stress linearized equivalent stress on the right side would be similar to the second graph, confirming that the extra 20% in the first graph is a penalty. Would I be right?
I guess my question boils down to asking whether there is a need to linearize the stress on the opposite side from a discontinuity where there is no peak stress? If so, the Div 2 linearization rules seem to result in a 20% phantom stress being added to the Von Mises Yield Criteria.
My understanding is that the purpose of Linearization is to remove the peak stress so that membrane and bending components can be found for each element of the stress tensor. Linearization according to ASME VIII Div 2 Annex 5-A is obviously applicable to the end of the stress classification line where the discontinuity (or pad) is.
However, I am wondering how to handle the stress at the other end of the stress classification line (the inside surface of the vessel). As there is no discontinuity or peak stress, is there a need to use the linearised M+B equivilant stress or can you use the "total" equivilant stress.
I ask because when linearizing in accordance with Div 2 using ANSYS 19.1 with through thickness bending set to Zero the following plot is the result. The blue membrane plus bending line looks good on the left where the discontinuity is. However it results in an equivilant stress that is 20% higher than the total equivilant stress on the right.
There are 3 stress components: Membrane, Bending and Peak. As there is no peak stress on the right, the blue Membrane Plus bending line should be very close to the brown total stress line. Why is the the blue line 20% higher? It looks like a conservative penalty to me.
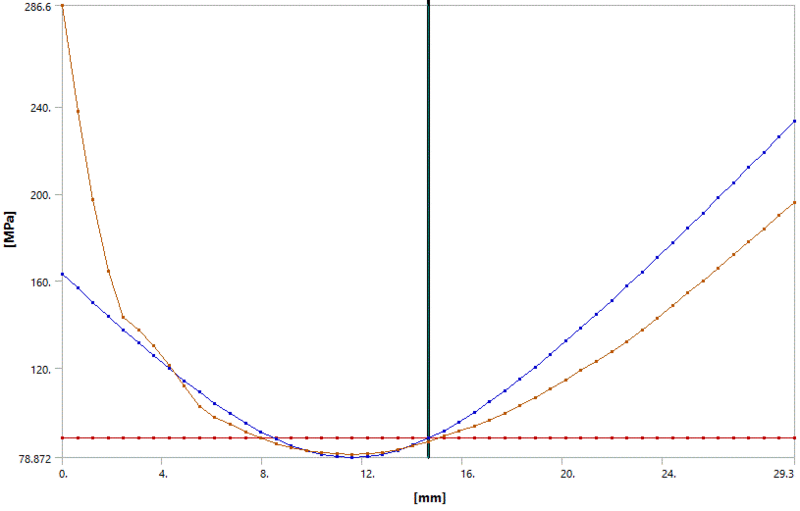
The following graph is for through thickness bending "not" set to Zero. It appears to produce a poorer quality result on the left but a good result that closely matches the total stress on the right.
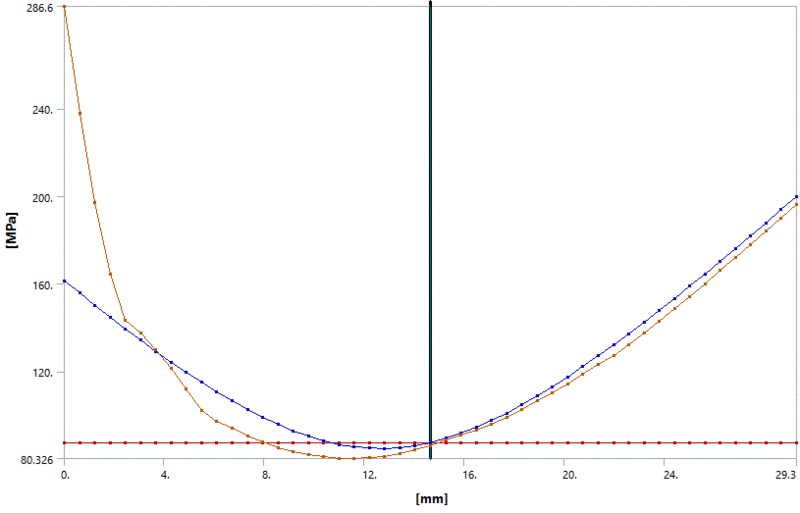
My suspicion is that if I was to model the geometry using shell elements, and apply the Div 2 shell element linearization rules then the stress linearized equivalent stress on the right side would be similar to the second graph, confirming that the extra 20% in the first graph is a penalty. Would I be right?
I guess my question boils down to asking whether there is a need to linearize the stress on the opposite side from a discontinuity where there is no peak stress? If so, the Div 2 linearization rules seem to result in a 20% phantom stress being added to the Von Mises Yield Criteria.