Hi Everyone,
When analyzing a box culvert I know the trend is to apply an equal but opposite upwards force on the bottom slab to model the reaction of the downwards forces and to place a pin support below the walls. (The assumption is that the soil below provides a uniform reaction force).
For a single cell box culvert, this method gives resulting moments and shears that are virtually identical (within 0.1%) to if you were to place soil springs underneath the bottom slab as the support conditions, and apply no external upwards reaction force.
Such conditions are shown below.
For the single cell culvert with pin supports, the equal but opposite upwards force in a net zero change at the supports, thus there is no reaction.
My question is how to go about this approach when modelling a double cell box culvert. If doing the method where an equal but opposite reaction is applied, is a pin support placed below the middle wall? or is it left out like shown below.
If a pin support support is placed below the middle wall it results in forces at the pin support (i.e. no net zero support forces), and moments and shears that are slightly different (5-10%) from that of a model that uses soil spring supports. See reactions below for supports below each wall.
If the middle pin support is not placed in the model, then the resulting moments and shears match up closer to that of the soil spring support condition.
Which method is the most realistic representation of the forces? A pin support under all three walls, under exterior wall only, or using soil springs?
I would think that by having a support under all three walls and getting different reaction forces, it isn't modelling it as accurately as it should be, since this no longer results in the assumption that the soil gives a uniform reaction force.
Thanks.
When analyzing a box culvert I know the trend is to apply an equal but opposite upwards force on the bottom slab to model the reaction of the downwards forces and to place a pin support below the walls. (The assumption is that the soil below provides a uniform reaction force).
For a single cell box culvert, this method gives resulting moments and shears that are virtually identical (within 0.1%) to if you were to place soil springs underneath the bottom slab as the support conditions, and apply no external upwards reaction force.
Such conditions are shown below.
For the single cell culvert with pin supports, the equal but opposite upwards force in a net zero change at the supports, thus there is no reaction.
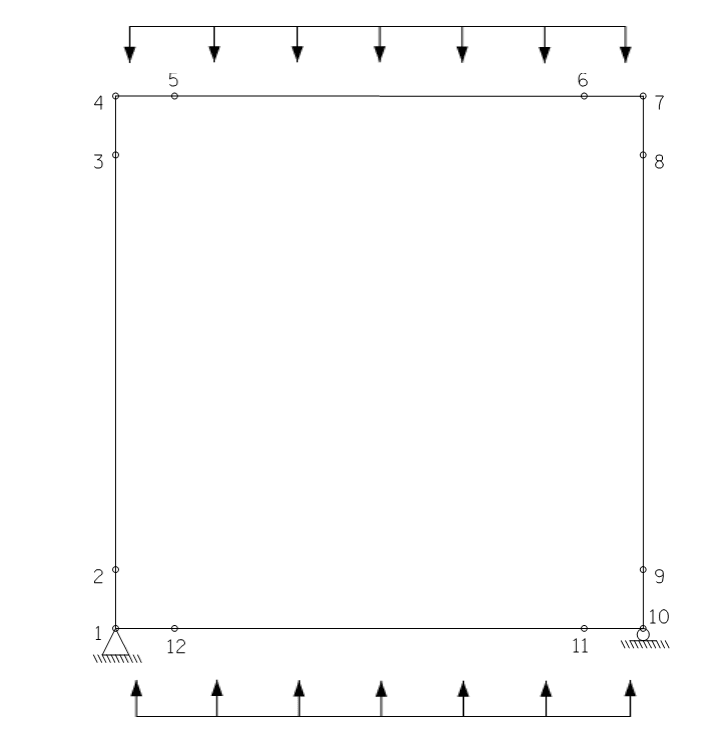
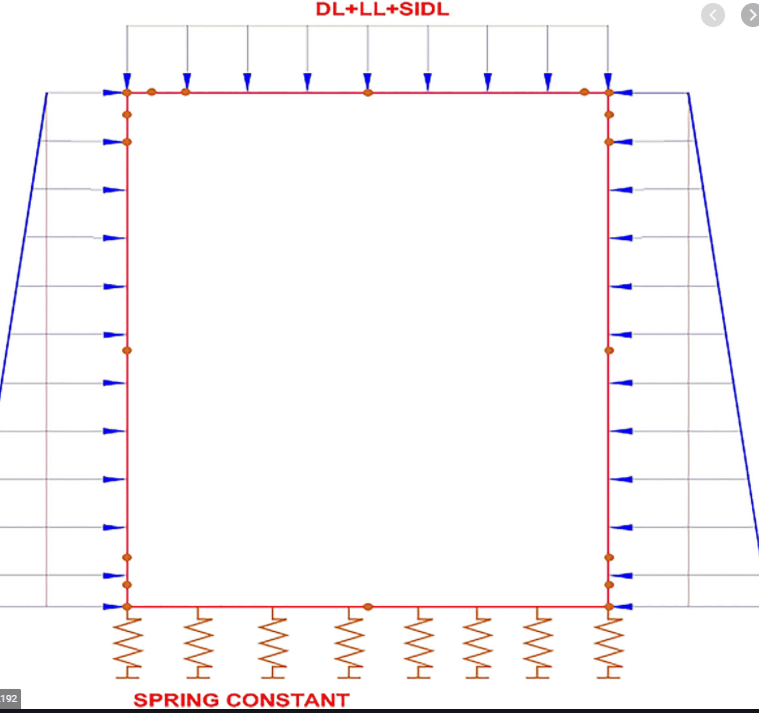
My question is how to go about this approach when modelling a double cell box culvert. If doing the method where an equal but opposite reaction is applied, is a pin support placed below the middle wall? or is it left out like shown below.
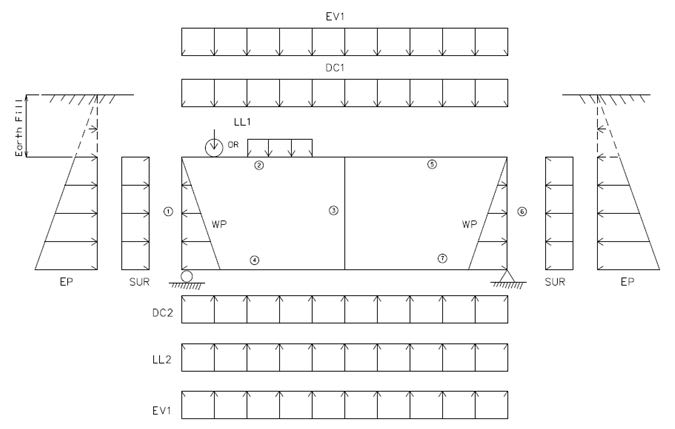
If a pin support support is placed below the middle wall it results in forces at the pin support (i.e. no net zero support forces), and moments and shears that are slightly different (5-10%) from that of a model that uses soil spring supports. See reactions below for supports below each wall.
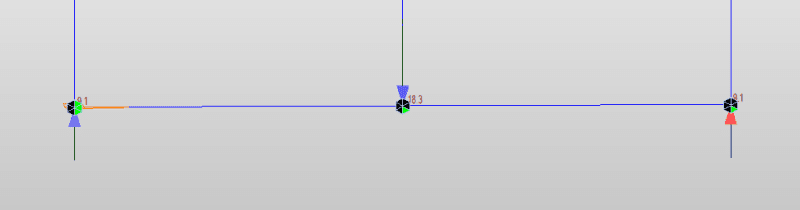
If the middle pin support is not placed in the model, then the resulting moments and shears match up closer to that of the soil spring support condition.
Which method is the most realistic representation of the forces? A pin support under all three walls, under exterior wall only, or using soil springs?
I would think that by having a support under all three walls and getting different reaction forces, it isn't modelling it as accurately as it should be, since this no longer results in the assumption that the soil gives a uniform reaction force.
Thanks.