Hi all,
I've been asked to assess whether it's acceptable to load I beam with several concentrated loads. The load is not high so in general, this seems fine. My concern is that the connection of the load is through eye bolts will be installed on the treaded hole tapping in the central of the flange to part of the web However, my concern lies with the method of attaching these loads. The loads will be connected through eye bolts installed in threaded holes located at the center of the flange, extending into the web. I’ve never encountered this type of connection before and am unsure if it’s acceptable. I was initially thinking about applying a reduction factor for the flange and web area based on the hole-cutting area, but I am not sure if there is safe enough. Is there anything I have missed?
Has anyone encountered a similar situation or found any code references that address limitations for such connections?
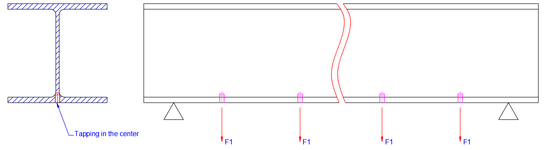
I considered offsetting the holes from the center line to create a zigzag pattern, but this would introduce a torsion to the beam in the segments. Between these two options, which one do you think is better? Thanks in advance.
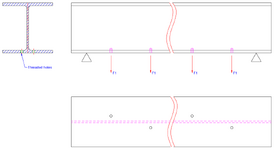
I've been asked to assess whether it's acceptable to load I beam with several concentrated loads. The load is not high so in general, this seems fine. My concern is that the connection of the load is through eye bolts will be installed on the treaded hole tapping in the central of the flange to part of the web However, my concern lies with the method of attaching these loads. The loads will be connected through eye bolts installed in threaded holes located at the center of the flange, extending into the web. I’ve never encountered this type of connection before and am unsure if it’s acceptable. I was initially thinking about applying a reduction factor for the flange and web area based on the hole-cutting area, but I am not sure if there is safe enough. Is there anything I have missed?
Has anyone encountered a similar situation or found any code references that address limitations for such connections?
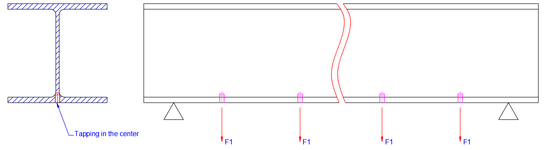
I considered offsetting the holes from the center line to create a zigzag pattern, but this would introduce a torsion to the beam in the segments. Between these two options, which one do you think is better? Thanks in advance.
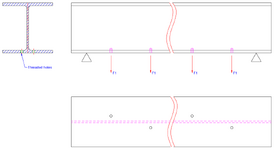