iam42
Industrial
- Feb 15, 2007
- 175
Guys,
I am really struggling on how to proceed with a weld procedure qualification that I am currently working on.
The material is 8" sch40 2205 Duplex. Our customer has a requirement for corrosion testing IAW ASTM G48 method A. His criteria for the test is testing at 35°C for 72 hours. The acceptance criteria is "No pitting or crevice corrosion in either the weld metal or HAZ is permitted"
I just received the test results and with my limited knowledge it does not look good. The test results are shown below.
If anyone know what is going wrong, I would really appreciate a push in the right direction!
Thanks
I am really struggling on how to proceed with a weld procedure qualification that I am currently working on.
The material is 8" sch40 2205 Duplex. Our customer has a requirement for corrosion testing IAW ASTM G48 method A. His criteria for the test is testing at 35°C for 72 hours. The acceptance criteria is "No pitting or crevice corrosion in either the weld metal or HAZ is permitted"
I just received the test results and with my limited knowledge it does not look good. The test results are shown below.
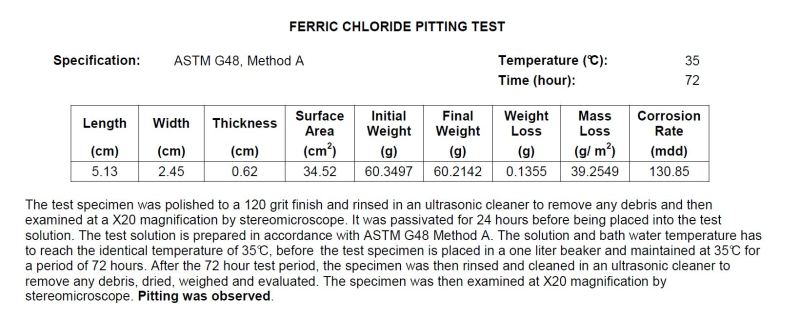
If anyone know what is going wrong, I would really appreciate a push in the right direction!
Thanks