Here is a question I thought I'd throw out to the masses. I'm after what people find as the most effective/economic solution to a structure of the form:
-Steel framed, open section beams and columns
-Braced frames for lateral restraint
-Multiple stories (let say 3-8 stories)
-Industrial setting envisaged so less architectural constraints.
Have you found benefits in using moment connections for the primary beams? Given there is already lateral restraint the benefits of the moment connection mostly lie in better economy of the relevant beams. A simple example is shown in the plan view below where all the beams running north-south are moment connections.
(Obviously most of use know the trade offs between moment connections and simply supported. Moment connections generally make more efficient use of your members but connection detailing can be more difficult both for engineering and cost of fabrication and erection. )
-Steel framed, open section beams and columns
-Braced frames for lateral restraint
-Multiple stories (let say 3-8 stories)
-Industrial setting envisaged so less architectural constraints.
Have you found benefits in using moment connections for the primary beams? Given there is already lateral restraint the benefits of the moment connection mostly lie in better economy of the relevant beams. A simple example is shown in the plan view below where all the beams running north-south are moment connections.
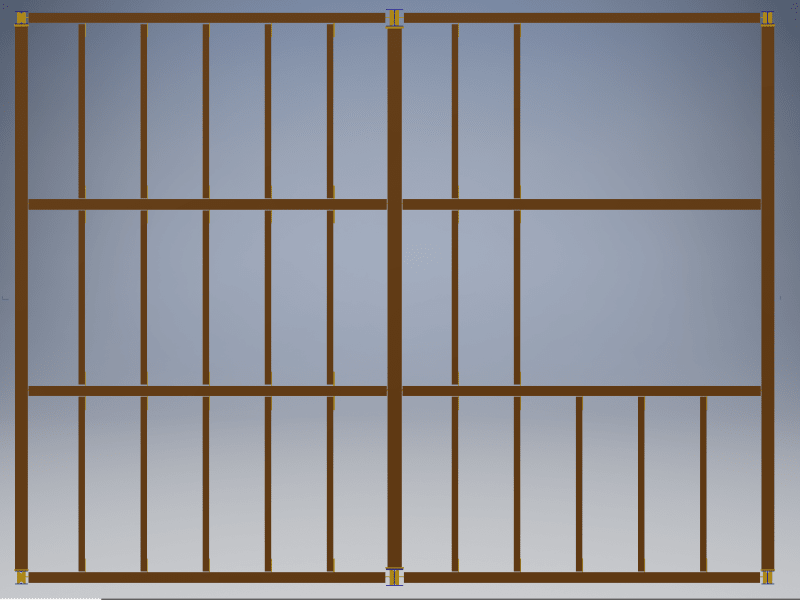
(Obviously most of use know the trade offs between moment connections and simply supported. Moment connections generally make more efficient use of your members but connection detailing can be more difficult both for engineering and cost of fabrication and erection. )