Hi
During normal operation, oil was dripping below our alternator 45 MW 11 kV. The oil comes from the bearing. During shutdown, a hydraulic pipe was replaced. Now still some oil is dripping.
Can the oil cause damage in the rotor and stator winding? Any other negative impact?
During normal operation, oil was dripping below our alternator 45 MW 11 kV. The oil comes from the bearing. During shutdown, a hydraulic pipe was replaced. Now still some oil is dripping.
Can the oil cause damage in the rotor and stator winding? Any other negative impact?
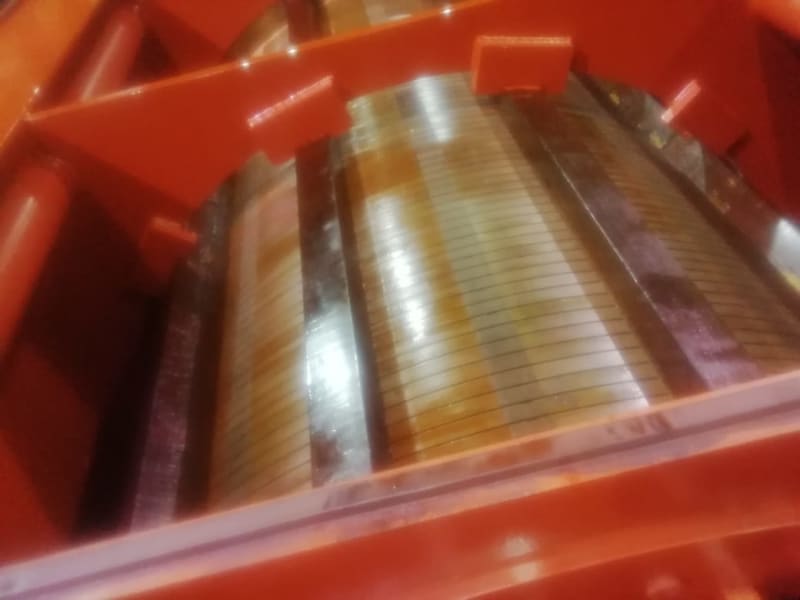
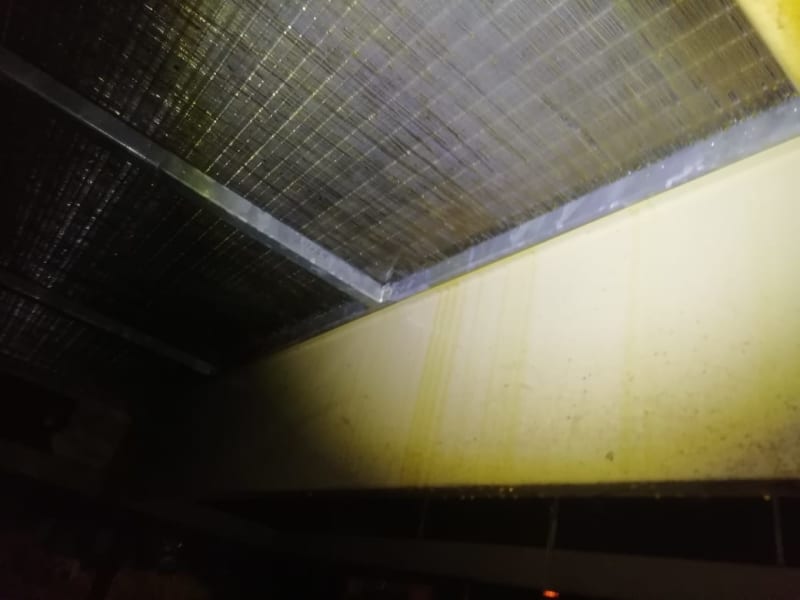
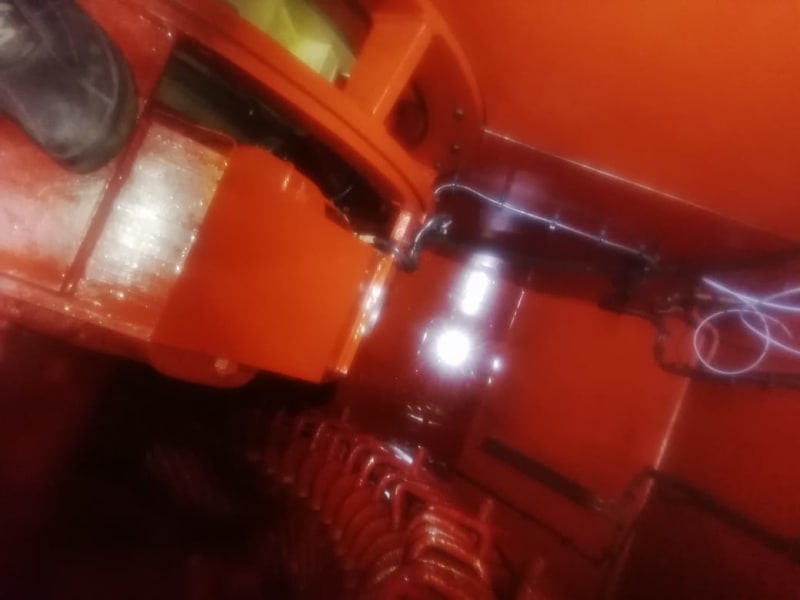
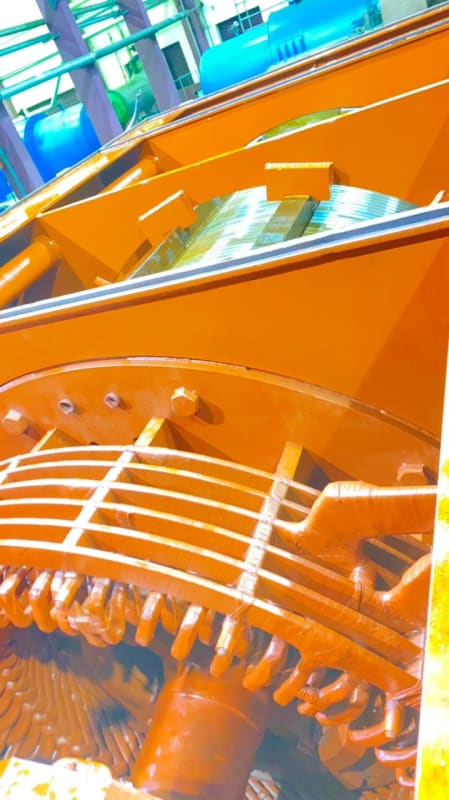