Ahmad Uzair Arshad
Civil/Environmental
Hi Fellow Engineers,
I was designing a raft for a mid rise 17 story residential tower, It was in my knowledge that Modelling Stiff element under column decreases the max moment because of decrease in clear span.
Even CSI knowledge base acknowledge that modelling of stiff element is a non conservative approach.
[link ][/url]
Anyway, I designed it without col-stiff element & raft is now casted already, Than one day out of curiosity I decided to check the effect of Col-Stiff Element & contrary to my knowledge at some Locations the bending moment values increased by a factor of around 1.5 even at service loads, now my nights are sleepless as this is inducing wide cracks at service & at ultimate cases provided reinforcement is inadequate.
Now theoretically this is not making much sense to me, also I don't see many the engineers use col-stiff approach in design.
Can anyone help me understand, what is happening here.
even the bending moment diagram is not making much sense for stiff element model, as bending moment is low under column of larger span.
for model without stiff elements bending moment diagram is more rational.
Thank you
I was designing a raft for a mid rise 17 story residential tower, It was in my knowledge that Modelling Stiff element under column decreases the max moment because of decrease in clear span.
Even CSI knowledge base acknowledge that modelling of stiff element is a non conservative approach.
[link ][/url]
Anyway, I designed it without col-stiff element & raft is now casted already, Than one day out of curiosity I decided to check the effect of Col-Stiff Element & contrary to my knowledge at some Locations the bending moment values increased by a factor of around 1.5 even at service loads, now my nights are sleepless as this is inducing wide cracks at service & at ultimate cases provided reinforcement is inadequate.
Now theoretically this is not making much sense to me, also I don't see many the engineers use col-stiff approach in design.
Can anyone help me understand, what is happening here.
even the bending moment diagram is not making much sense for stiff element model, as bending moment is low under column of larger span.
for model without stiff elements bending moment diagram is more rational.
Thank you
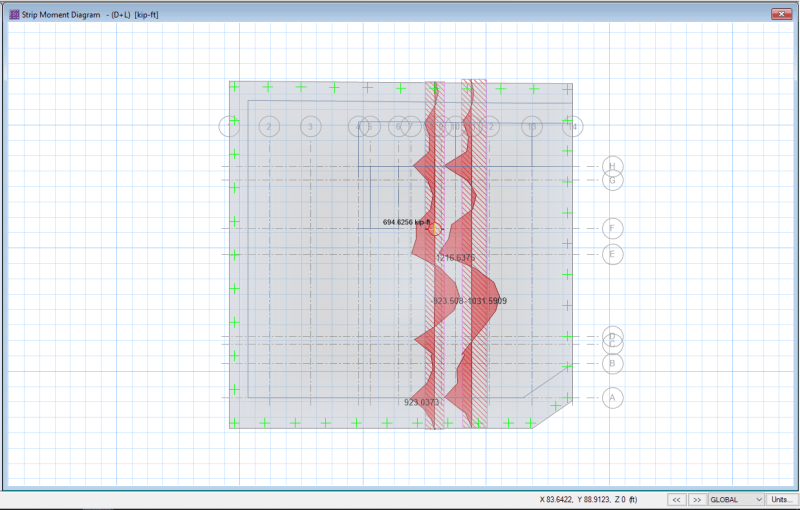
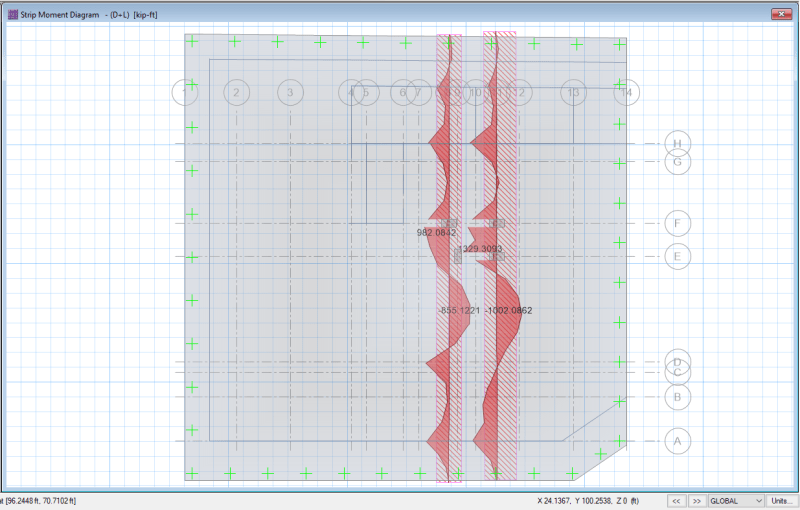