hi
im doing an elastic plastic analysis using ansys. for the material model i used asme sec VIII div2 model.
i have formulated it in excel and double checked it and it's correct.plastic strain at yield point is not zero (gamma_1+gamma_2), why ?[highlight #FCE94F][/highlight] what must i do ? in ansys i have to enter zero plastic strain at yield point.
for the stresses after yield which values i have to enter in ansys material model ? just the plastic portion (gamma_1 + gamma_2)?
what is the right procedure ?
thanks in advance.
im doing an elastic plastic analysis using ansys. for the material model i used asme sec VIII div2 model.
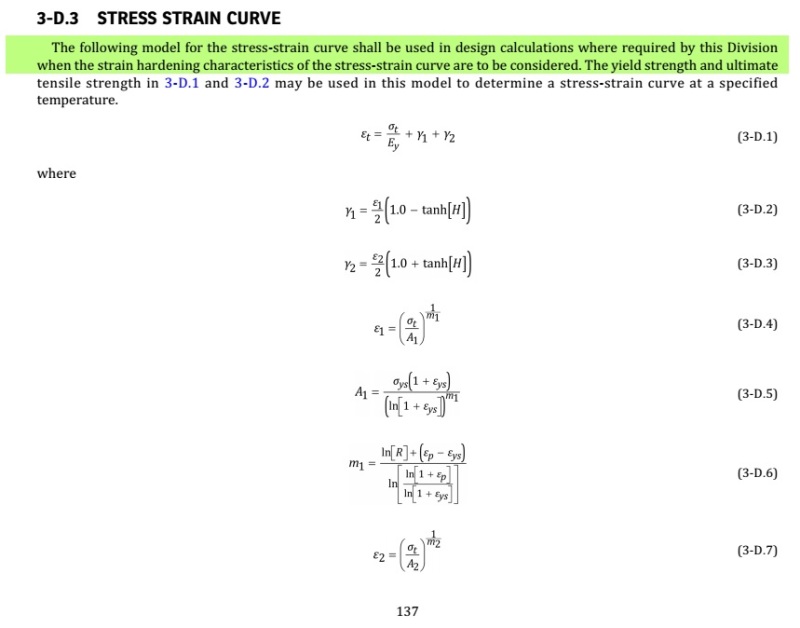
i have formulated it in excel and double checked it and it's correct.plastic strain at yield point is not zero (gamma_1+gamma_2), why ?[highlight #FCE94F][/highlight] what must i do ? in ansys i have to enter zero plastic strain at yield point.
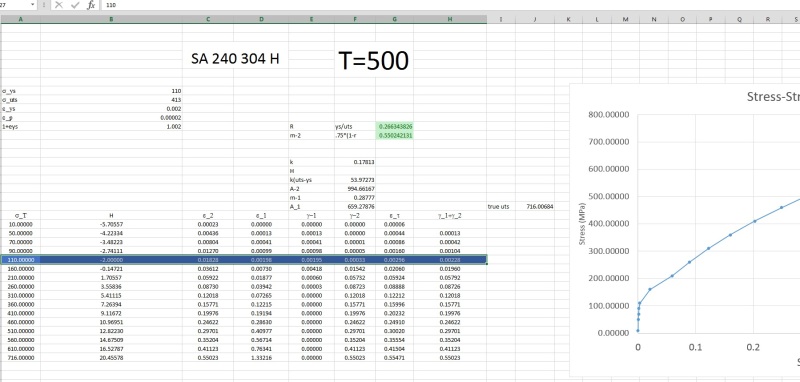
for the stresses after yield which values i have to enter in ansys material model ? just the plastic portion (gamma_1 + gamma_2)?
what is the right procedure ?
thanks in advance.