Dears,
I would like to understand which temperatures to consider according to the following paragraph of EN 13445 for the calculation of fixed tubesheets heat exchangers:
The code mentions normal operating conditions, the start-up conditions, the shut-down conditions, the upset and the pressure test conditions. Our software automatically defines the following temperatures (as wall temperatures) and the following loading cases (based on the 4 temperatures filled in input):
For each of these conditions it performs the calculation correctly by differentiating for the 7 loading cases.
My first doubt concerns the upset conditions: what temperatures should be considered? Are these conditions mandatory per EN 13445?
Second doubt: according to what I have found in this article , one should always specify (based on the output of the thermal calculation) the actual wall temperatures defined on the basis of the properties of the fluids and how they actually transmit heat. From this I understand the simplicity (not always having the full thermal calculation available) of averaging the 4 temperatures, which is certainly not correct. How do the software you use take into account the temperatures in the table in our software?
Third doubt: we have to design the exchanger having the following temperatures
SHELL SIDE IN/OUT 40/219.4
TUBE SIDE IN/OUT 257/105
Design pressure = 30 barg + FV each side
Design temperature = 280 °C each side
I have designed more than 50 exchangers with fixed tubesheets, but now I cannot find a combination of thicknesses that satisfies all the equations in the code, so all the doubts about these loading cases have arisen.
Can you help me?
Thanks in advance
I would like to understand which temperatures to consider according to the following paragraph of EN 13445 for the calculation of fixed tubesheets heat exchangers:
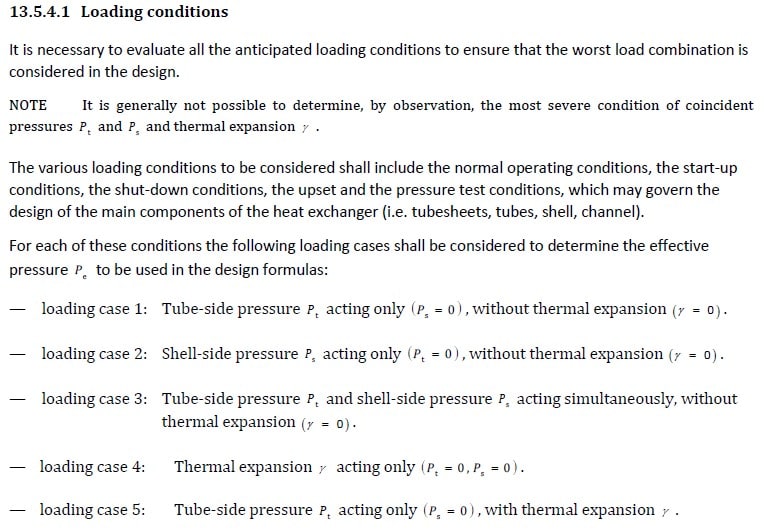
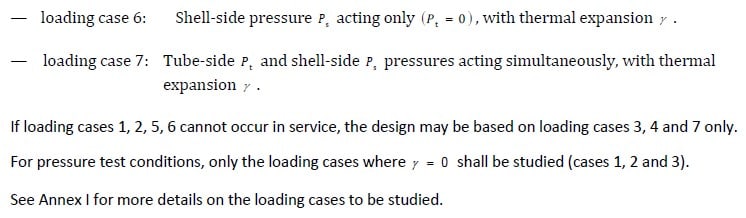
The code mentions normal operating conditions, the start-up conditions, the shut-down conditions, the upset and the pressure test conditions. Our software automatically defines the following temperatures (as wall temperatures) and the following loading cases (based on the 4 temperatures filled in input):
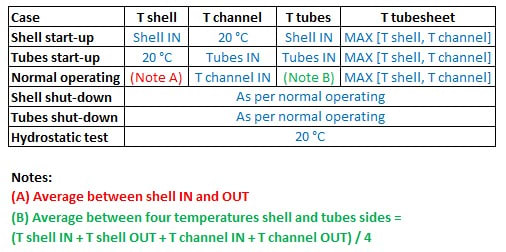
For each of these conditions it performs the calculation correctly by differentiating for the 7 loading cases.
My first doubt concerns the upset conditions: what temperatures should be considered? Are these conditions mandatory per EN 13445?
Second doubt: according to what I have found in this article , one should always specify (based on the output of the thermal calculation) the actual wall temperatures defined on the basis of the properties of the fluids and how they actually transmit heat. From this I understand the simplicity (not always having the full thermal calculation available) of averaging the 4 temperatures, which is certainly not correct. How do the software you use take into account the temperatures in the table in our software?
Third doubt: we have to design the exchanger having the following temperatures
SHELL SIDE IN/OUT 40/219.4
TUBE SIDE IN/OUT 257/105
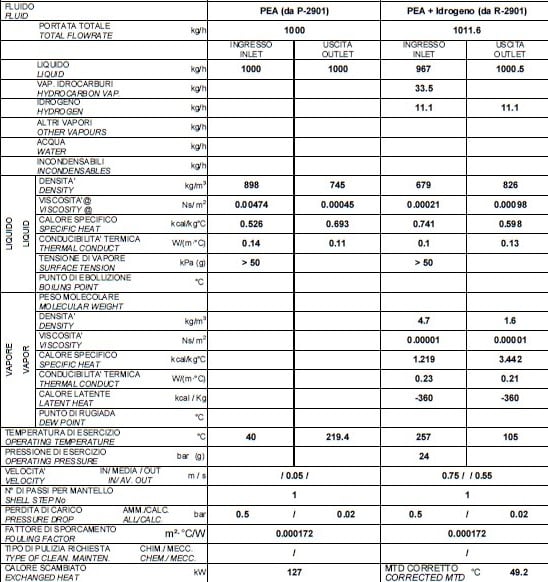
Design pressure = 30 barg + FV each side
Design temperature = 280 °C each side
I have designed more than 50 exchangers with fixed tubesheets, but now I cannot find a combination of thicknesses that satisfies all the equations in the code, so all the doubts about these loading cases have arisen.
Can you help me?
Thanks in advance