julian89
Mechanical
- Nov 11, 2013
- 33
Good day ladies and gentlemen!
Say one has a buckled tube (or any other component for that matter), and want to estimate the strains present, how would one go about that using FEA?
My attempt, as it stands, was to do a buckling analysis with, with a proper scaling, such that the shapes of the FEA model and the real component look visually similar. My approach is exactly the same as that described in this video: Link
However, with the last static structural analysis, one only get's the strains relative to the buckled shape, right? So if the loading on the last static structural analysis is 0, the strains will be 0.
How would you go about solving this?
Thanks for any eng-tips. Wish you all an awesome day!
I'm using ANSYS 19.0.
Setup in Workbench:
An example (not mine):
Say one has a buckled tube (or any other component for that matter), and want to estimate the strains present, how would one go about that using FEA?
My attempt, as it stands, was to do a buckling analysis with, with a proper scaling, such that the shapes of the FEA model and the real component look visually similar. My approach is exactly the same as that described in this video: Link
However, with the last static structural analysis, one only get's the strains relative to the buckled shape, right? So if the loading on the last static structural analysis is 0, the strains will be 0.
How would you go about solving this?
Thanks for any eng-tips. Wish you all an awesome day!
I'm using ANSYS 19.0.
Setup in Workbench:
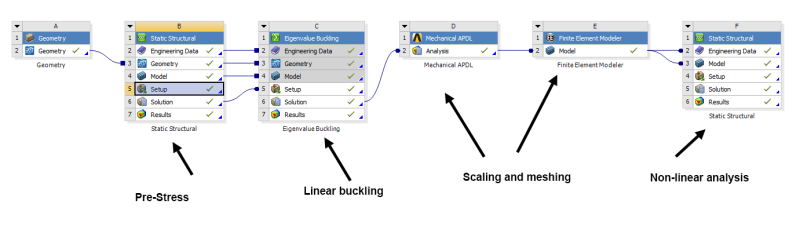
An example (not mine):
