FEMbiaatch
Mechanical
I'm working on the simulation of needle penetration into a thermoplastic polyurethane foil (0.4mm thick) using cohesive interaction behavior between two parts of a phantom corresponding to the outer diameter of the cutting edges of the needle tip. As for the model, I'm using a symmetric model by considering a needle to be a rigid part with frictionless contact between the surfaces. The mesh of the phantom is relatively coarse to keep the stable time inc to be reasonable. I have performed uniaxial tensile and relaxation tests on the material to be calibrated into the model. The model runs smoothly when I consider the phantom to be Neo Hookean hyperelastic material with incompressibility, but I obtain excessive distortion error with the Ogden hyperelastic model, which would be a better fit for the material. What would be the reason for such behavior? Any input would be much appreciated. Thanks!
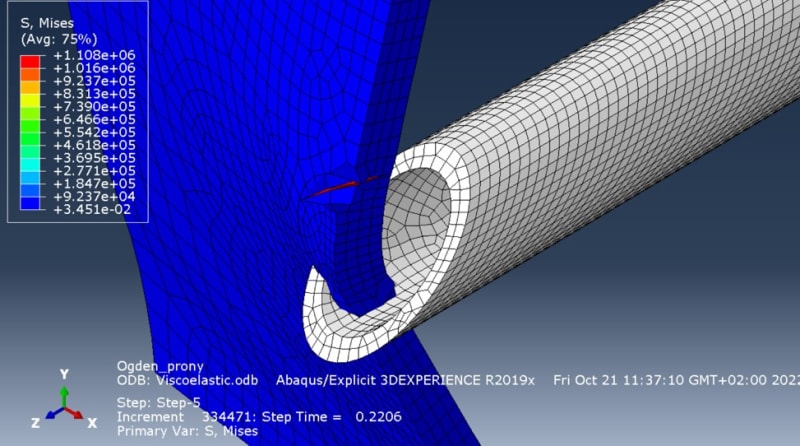
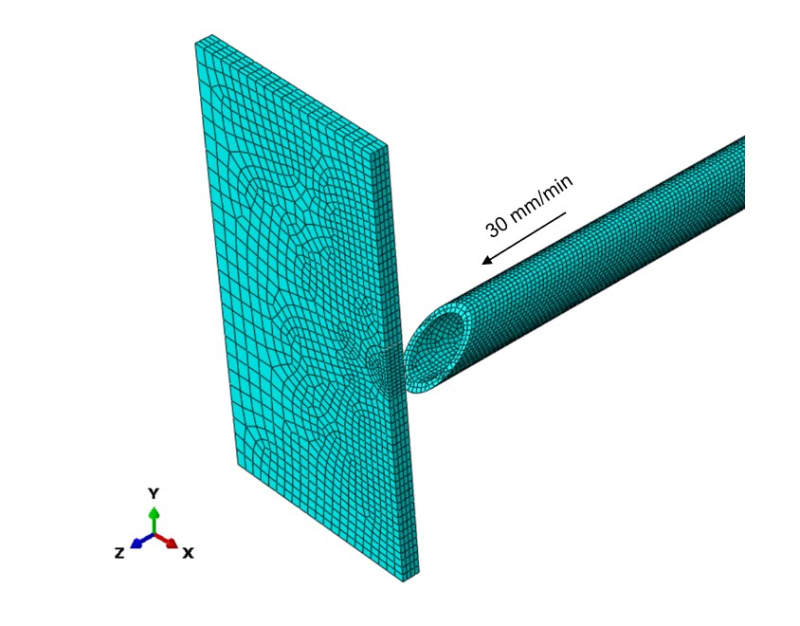
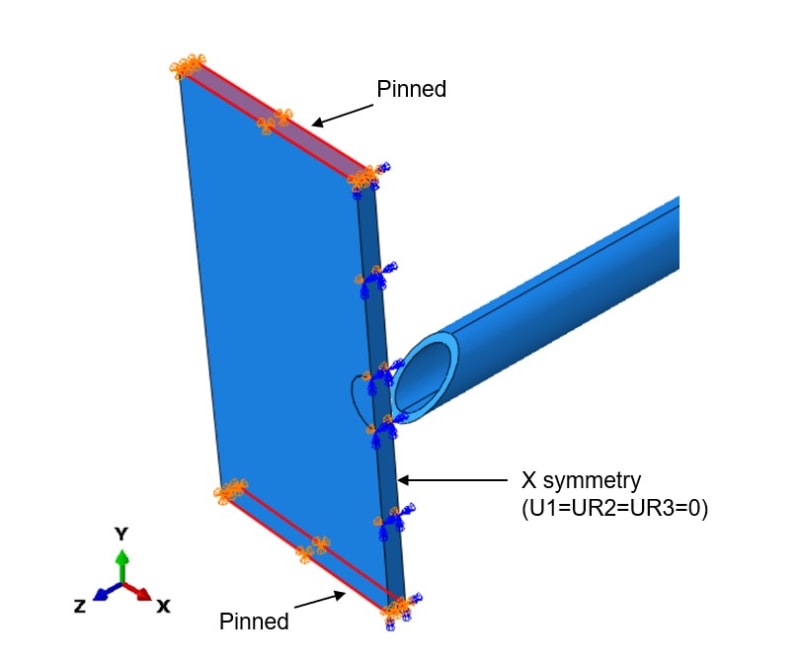