Would like to get some feedback on this. Client has an approx. 27' long LVL beam across his family room to bear the second floor joists above. The beam currently breaks over a bearing post at approx. 9'. The client would like to remove the bearing post.
Another engineer wrote a report for the client saying that the post can be removed and a 1/4" steel saddle is to be installed at the bottom of the existing beam, basically "cupping" the beam up to the bottom of the existing floor joists. The city plan reviewer asked for some calculations showing that this solution works, but the engineer said he can't do that. Client came to us to ask if we could do it. By transforming the proposed steel saddle into an equivalent wood beam I feel that I'm able to prove that it would work for bending and deflection. If the wood beam was continuous then it would work in shear on its own without the steel saddle. But it isn't continuous as noted on the drawing below.
So what do you all think? Is this a fool's errand? Obviously we could either remove the beam and replace it, or cut off the bottom part of the existing beam and put in a new dropped steel beam. But if this saddle could work the client would prefer it for obvious reasons. I'm just not sure I have the tools or know-how to figure out what happens at that break in the beam. Any thoughts or advice would be greatly appreciated.
Another engineer wrote a report for the client saying that the post can be removed and a 1/4" steel saddle is to be installed at the bottom of the existing beam, basically "cupping" the beam up to the bottom of the existing floor joists. The city plan reviewer asked for some calculations showing that this solution works, but the engineer said he can't do that. Client came to us to ask if we could do it. By transforming the proposed steel saddle into an equivalent wood beam I feel that I'm able to prove that it would work for bending and deflection. If the wood beam was continuous then it would work in shear on its own without the steel saddle. But it isn't continuous as noted on the drawing below.
So what do you all think? Is this a fool's errand? Obviously we could either remove the beam and replace it, or cut off the bottom part of the existing beam and put in a new dropped steel beam. But if this saddle could work the client would prefer it for obvious reasons. I'm just not sure I have the tools or know-how to figure out what happens at that break in the beam. Any thoughts or advice would be greatly appreciated.
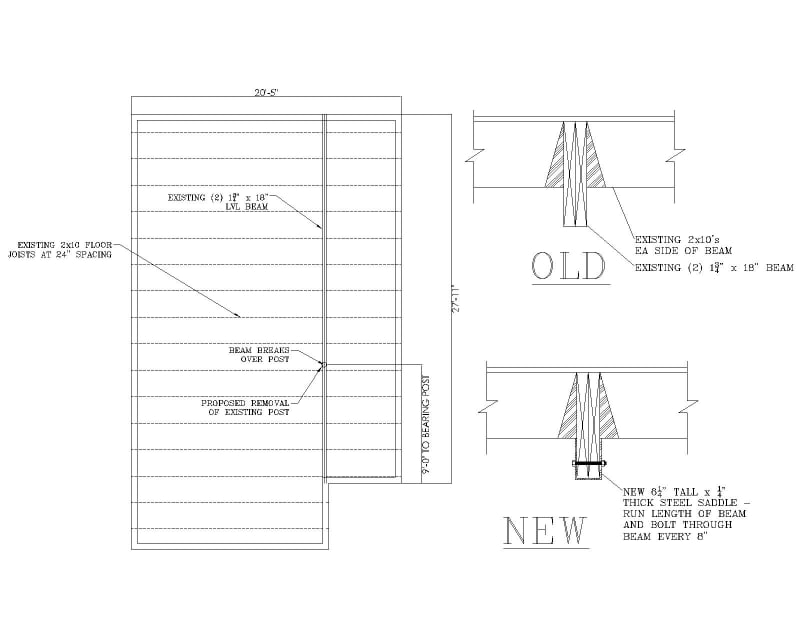