Phil121324
Mechanical
Hi,
Hopefully i have posted this in the correct area, apologies if not- Send me in the right direction...
I am looking at the failure of a valve stem from a control valve, the stem has sheared during valve operation, the failure has occurred at the first thread at the bottom of the stem, the first weakest point, the thread connects the valve plug to the stem. In short the stem connects the plug within the valve body to the actuator, this then allows the control valve to control the pressure in the system. The stem material is SS 316, the valve works on a FWKO system ( at around 40 bar.
In normal operating conditions the stem sees very little tension (i am assuming failure in tension), if the valve is incorrectly setup the stem can be subject to tension, if the stem receives the full tension that the actuator can deliver the yield strength of the material is surpassed by around 20% however the UTS is still well within. As the stem is seeing tension my initial thoughts were not to be too concerned with the yield strength of the material and look at the UTS.
I have attached a photo of the failed shaft- can anyone shed some light on the type of failure or point me in the right direction. Could the failure be hydrogen embrittlement, a brittle fracture of a relatively ductile material.
thanks
Phil
Hopefully i have posted this in the correct area, apologies if not- Send me in the right direction...
I am looking at the failure of a valve stem from a control valve, the stem has sheared during valve operation, the failure has occurred at the first thread at the bottom of the stem, the first weakest point, the thread connects the valve plug to the stem. In short the stem connects the plug within the valve body to the actuator, this then allows the control valve to control the pressure in the system. The stem material is SS 316, the valve works on a FWKO system ( at around 40 bar.
In normal operating conditions the stem sees very little tension (i am assuming failure in tension), if the valve is incorrectly setup the stem can be subject to tension, if the stem receives the full tension that the actuator can deliver the yield strength of the material is surpassed by around 20% however the UTS is still well within. As the stem is seeing tension my initial thoughts were not to be too concerned with the yield strength of the material and look at the UTS.
I have attached a photo of the failed shaft- can anyone shed some light on the type of failure or point me in the right direction. Could the failure be hydrogen embrittlement, a brittle fracture of a relatively ductile material.
thanks
Phil
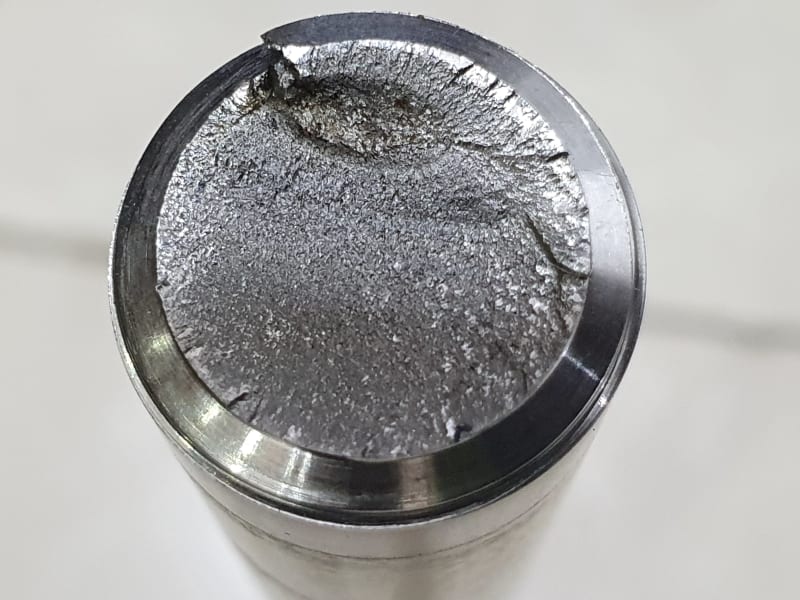