I have a long fancy door that weighs roughly 1000lbs (total weight over 23 linear feet) that will be hung from my structural steel lintel (HSS 12"x8"x1/2"). I'm the steel subtrade / delegated designer but as a favor to the GC I am designing the bulkhead attachment for the window contractor since they won't do it. Loads are low but it's a real, real fancy door and the window contractor has been sparse with details. I would rather overkill this thing than have any issues in service. What I'm looking for is help with is the following:
1. What fasteners to use through the 3/4" ply to the structural steel. Drilling is a given due to the thickness of lintel. Need low profile head since I don't want to recess too much as that'll possibly lead to pull-through of the outer 3/4" ply. Anything Hilti is preferred (easy to procure) but PAFs will not work per the window contractor (head sticks out too much)
2. How to handle the two ply problem (i.e. how worried am I about these separating and what measures should be taken to ensure they act together)
3. Anything else I need to know about fancy sliding doors. Peculiarities with fancy stuff is something I don't have too much experience with.
Figure 1: This is from Window contractor's shop drawings. Apparently their standard is 2-plies of 3/4" ply with wood screws through their track. Not sure why a single piece of lumber won't work but they're adamant about the two 3/4 plies. They have no idea about the spacing of their attachments, so I'll probably work backwards to see what the max span is for the 3/4" plies (assuming one fastener per panel - should be conservative - or max capacity of a single wood screw) and state that as max fastener spacing on the drawing.
Figure 2: Kind of what I was envisioning. I put screws as 16" c/c as a placeholder for now but as mentioned above will check max span of a single 3/4" ply. To get the two 3/4" plies to work together was going to wood screw them and use adhesive between the plies. Stagger joints.
1. What fasteners to use through the 3/4" ply to the structural steel. Drilling is a given due to the thickness of lintel. Need low profile head since I don't want to recess too much as that'll possibly lead to pull-through of the outer 3/4" ply. Anything Hilti is preferred (easy to procure) but PAFs will not work per the window contractor (head sticks out too much)
2. How to handle the two ply problem (i.e. how worried am I about these separating and what measures should be taken to ensure they act together)
3. Anything else I need to know about fancy sliding doors. Peculiarities with fancy stuff is something I don't have too much experience with.
Figure 1: This is from Window contractor's shop drawings. Apparently their standard is 2-plies of 3/4" ply with wood screws through their track. Not sure why a single piece of lumber won't work but they're adamant about the two 3/4 plies. They have no idea about the spacing of their attachments, so I'll probably work backwards to see what the max span is for the 3/4" plies (assuming one fastener per panel - should be conservative - or max capacity of a single wood screw) and state that as max fastener spacing on the drawing.
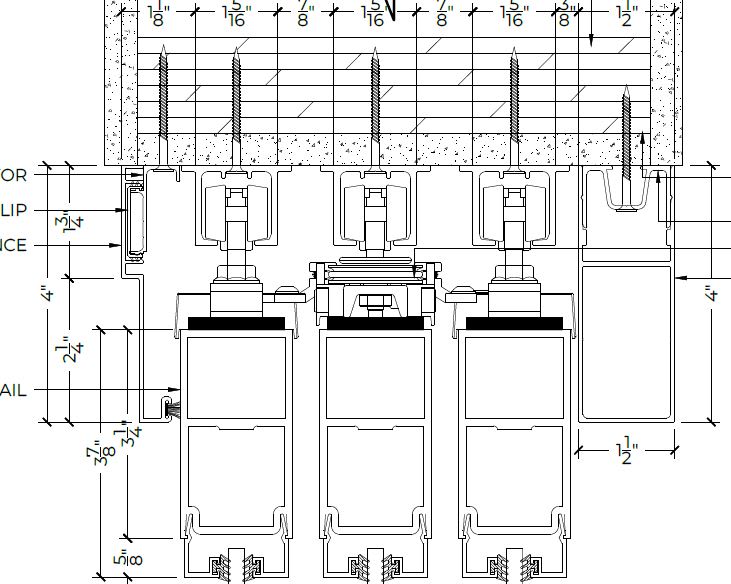
Figure 2: Kind of what I was envisioning. I put screws as 16" c/c as a placeholder for now but as mentioned above will check max span of a single 3/4" ply. To get the two 3/4" plies to work together was going to wood screw them and use adhesive between the plies. Stagger joints.
