Krzsiek2552
Mechanical
Hi.
I need to carry out analysis of stress of kayak paddle. I'm sure that applied force is not to high because I found information about this in many articles. I applied the boundary condition as is shown in below.
The stress in the shaft is about 350 MPa while it should be no higher than about 120 MPa. Can anybody help me ? I will be really helpful as this is my MSc project and deadline is coming and I have no more idea what BC should I apply to obtain lower stress.
I attach also files needed to run this model in abaqus
I need to carry out analysis of stress of kayak paddle. I'm sure that applied force is not to high because I found information about this in many articles. I applied the boundary condition as is shown in below.
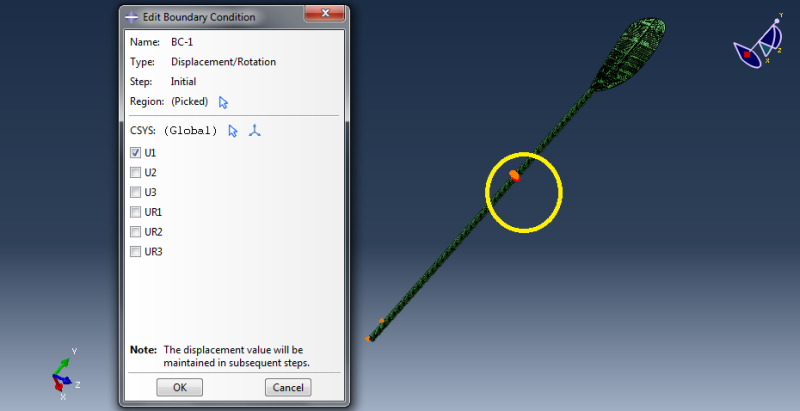
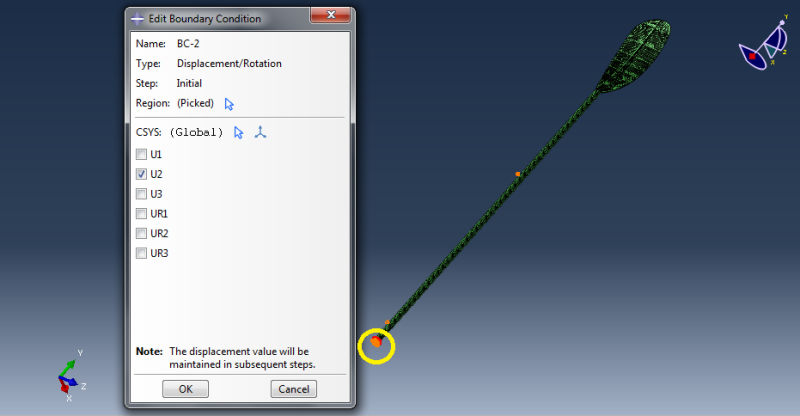
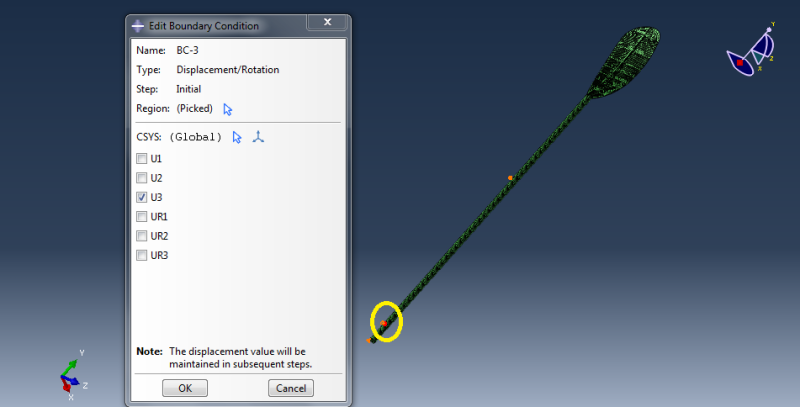
The stress in the shaft is about 350 MPa while it should be no higher than about 120 MPa. Can anybody help me ? I will be really helpful as this is my MSc project and deadline is coming and I have no more idea what BC should I apply to obtain lower stress.
I attach also files needed to run this model in abaqus