At my facility, we are currently lining 5 sumps (35' deep x 13.75' wide x 47' length) with stainless steel liner. Essentially, these are field fabricated 316 SS tanks built inside sumps. The sheet is 0.125 and most of it is 10' w x 4' high in size. At the horizontal seems, there are 0.25 inch thick straps with anchor bolts every 6 inches. The vertical seems have 2" wide straps with no anchors. The sheet is laid against the sump walls and floors which are 18" thick steel reinforced concrete. We also have 14 weep holes per sump to monitor for lining failure (2 on the floor, 12 on the walls). I have included an iso cut for reference.
Each sump has ~ 1 mile of weld. The QA/QC included visual, dye pen, and vac boxing. Sump 1 has failed three hydro tests and sump 2 has failed twice. All failures resulted from water flowing from the weep holes underneath the floor. Sump 1 is currently on the fourth go around of QA/QC inspection. The contractor has tried putting air behind the sheet (both with and without water in the sumps) to see if bubbles appeared or air leakage was detected, but they didn't. They never built any pressure behind the sheet, so we suspect all the air was making its way to the top and escaping through an unsealed area. They hired a 3rd party CWI to reinspect, which resulted in nothing found. They are going to try ultrasonic testing today to see if they can detect leakage locations. X-ray is out of the question because of the concrete behind the sheet.
Anyone have experience with a situation like this and/or have thoughts on other methods to detect leaks?
Each sump has ~ 1 mile of weld. The QA/QC included visual, dye pen, and vac boxing. Sump 1 has failed three hydro tests and sump 2 has failed twice. All failures resulted from water flowing from the weep holes underneath the floor. Sump 1 is currently on the fourth go around of QA/QC inspection. The contractor has tried putting air behind the sheet (both with and without water in the sumps) to see if bubbles appeared or air leakage was detected, but they didn't. They never built any pressure behind the sheet, so we suspect all the air was making its way to the top and escaping through an unsealed area. They hired a 3rd party CWI to reinspect, which resulted in nothing found. They are going to try ultrasonic testing today to see if they can detect leakage locations. X-ray is out of the question because of the concrete behind the sheet.
Anyone have experience with a situation like this and/or have thoughts on other methods to detect leaks?
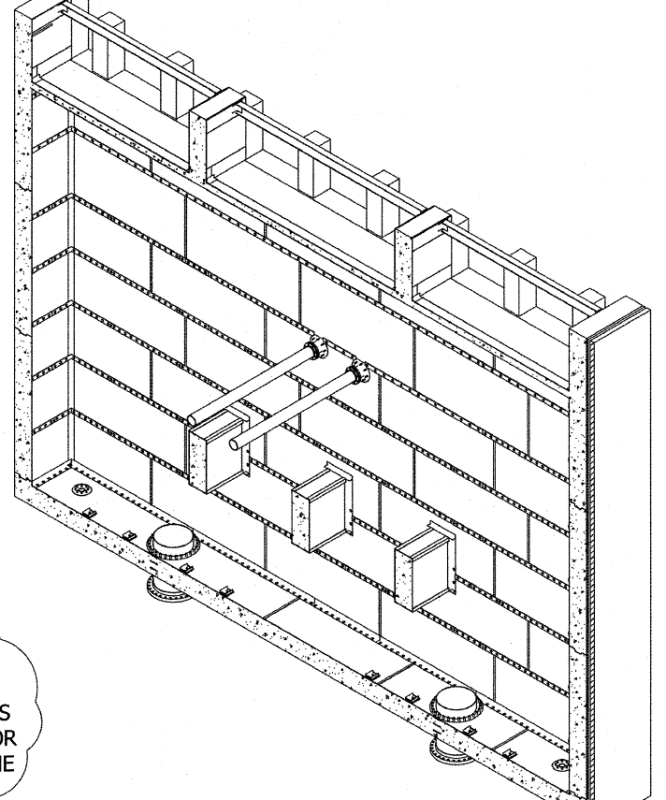