I am preparing drawings of a cable. The figure is something I threw together so that I could ask a question.
In the figure above, my datum features are the one receptacle. I am showing profile and positional tolerances for the opposite receptacle, but what I can really calling up is the force required to position it. The cable is flexible.
Would it make sense to call up profile and positional tolerances as zero? I am sure it will scare the heck out of the cable builder, but I am interested in meaning.
--
JHG
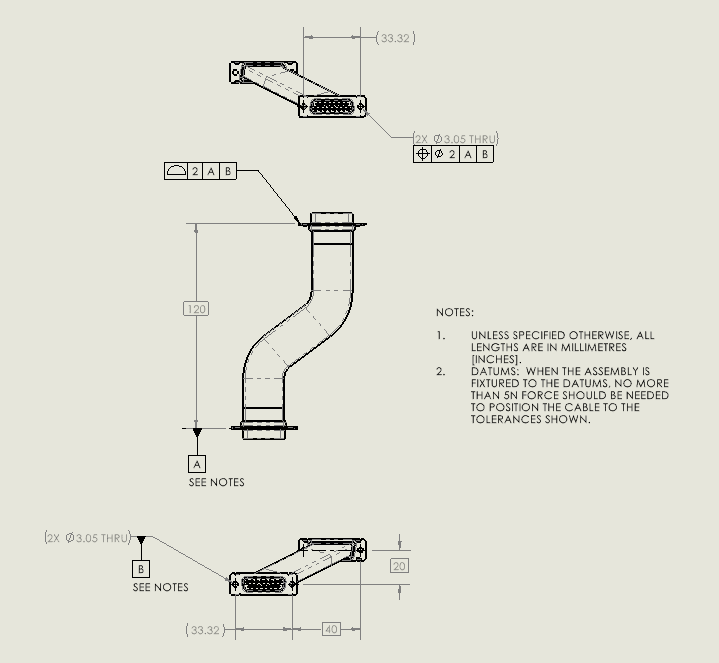
In the figure above, my datum features are the one receptacle. I am showing profile and positional tolerances for the opposite receptacle, but what I can really calling up is the force required to position it. The cable is flexible.
Would it make sense to call up profile and positional tolerances as zero? I am sure it will scare the heck out of the cable builder, but I am interested in meaning.
--
JHG