My problem is I have this pressure relief prop valve.
RS416-10/315/0,7
In the documentation it’s says it the maximum flow is 6 liter/minute depending on the nozzle D12.
Which is placed between the P port and the valve cone and then to the T tank.
You can buy it without the nozzle but ours have the R900008869 Nozzle 0.7 M4x7 MS RN115.38
The nozzles available are 0.7 mm, 0.8, 1, 1.1, 1.2, 1.4, 1.5, 1.6 mm
Since I cannot find any information in the document about the area without a nozzle,
My first assumption is that you cannot use the valve without one.
My second assumption is that the flow 6 l/min is the flow with a 1.6 mm nozzle.
My third assumption is that the flow is linear against the area, which means that a flowchart would look like this.
3 liter/minute and 1 mm2..
Nozzle Area Max Flow
0,7 0,38 1,15
0,8 0,50 1,5
1 0,79 2,34
1,1 0,95 2,84
1,2 1,13 3,38
1,4 1,54 4,59
1,5 1,77 5,27
1,6 2,01 6
Someone please tell me if this is correct!
It feels a bit to simple, makes me think I have missed or misunderstood something?
Something that adds to this confusion is that the valve is constructed in 1982, and someone working for the manufacturing company had a couple of years ago, looked at our valve and written that the maximum flow is 4 liter/minute.
And I do not understand how he came up with that number![[ponder] [ponder] [ponder]](/data/assets/smilies/ponder.gif)
This is not my area of expertise..
Best regards A
“Logic will get you from A to Z; imagination will get you everywhere.“
Albert Einstein
RS416-10/315/0,7
In the documentation it’s says it the maximum flow is 6 liter/minute depending on the nozzle D12.
Which is placed between the P port and the valve cone and then to the T tank.
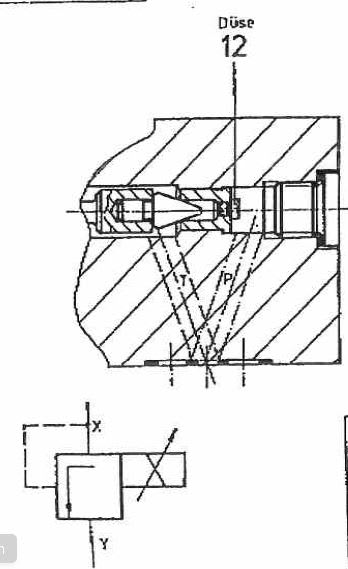
You can buy it without the nozzle but ours have the R900008869 Nozzle 0.7 M4x7 MS RN115.38
The nozzles available are 0.7 mm, 0.8, 1, 1.1, 1.2, 1.4, 1.5, 1.6 mm
Since I cannot find any information in the document about the area without a nozzle,
My first assumption is that you cannot use the valve without one.
My second assumption is that the flow 6 l/min is the flow with a 1.6 mm nozzle.
My third assumption is that the flow is linear against the area, which means that a flowchart would look like this.
3 liter/minute and 1 mm2..
Nozzle Area Max Flow
0,7 0,38 1,15
0,8 0,50 1,5
1 0,79 2,34
1,1 0,95 2,84
1,2 1,13 3,38
1,4 1,54 4,59
1,5 1,77 5,27
1,6 2,01 6
Someone please tell me if this is correct!
It feels a bit to simple, makes me think I have missed or misunderstood something?
Something that adds to this confusion is that the valve is constructed in 1982, and someone working for the manufacturing company had a couple of years ago, looked at our valve and written that the maximum flow is 4 liter/minute.
And I do not understand how he came up with that number
![[ponder] [ponder] [ponder]](/data/assets/smilies/ponder.gif)
This is not my area of expertise..
Best regards A
“Logic will get you from A to Z; imagination will get you everywhere.“
Albert Einstein