I have a line of fitness equipment that has had a small issue for some time, and now that all the bigger issues are out of the way it is time to tackle the small stuff. We have noticed that the belt side of the flywheel housing is being worn out after about a year's worth of service on a small percentage of units. The flywheel is spinning less than 500RPM. The bearings are 6001ZZ. The flywheels are cut on CNC, balanced, and inspected. Most of the radial load is coming from belt tension alone, but some comes from the eddy current resistance. This unit does not product a lot of resistance as it is a cardio piece. After the housing becomes worn the unit will make all sorts of bear rattle noises and if left unchecked, it eventually creates a thin wall condition with the belt grooves and brakes the flange lip right at the centerline of the bearing essentially locking the unit up completely. The bearings feel completely fine when removed so I do not think it stems from a bearing failure. I believe we have narrowed down the what; the bearing not initially being a tight fit even though it passed inspections. But I am still foggy as to the exact why. The exact why I think would be either the bearing bore was too loose all together (should not have passed inspection), allowing the bearing to walk slightly in the pocket. This would slowly wear away the casting. My other thought is the the surface finish is too rough in the bearing pocket, so it would be like pressing a bearing into a very fine threaded body. This would not hold the bearing well and could eventually wear the housing. The few things I can think of to help stop this from happening are; increase the wall thickness at that bearing site, increase the surface finish, add bearing loctite (similar to loctite 641) only on the outer race, and source a longer bearing so that there is more bearing surface between the bearing and flywheel.
Now to my main question. Does this sound like the correct direction or maybe someone has seen similar issues that they could shed some light on some possibilities that I have not thought of? Any incite would be much appreciated.
Now to my main question. Does this sound like the correct direction or maybe someone has seen similar issues that they could shed some light on some possibilities that I have not thought of? Any incite would be much appreciated.
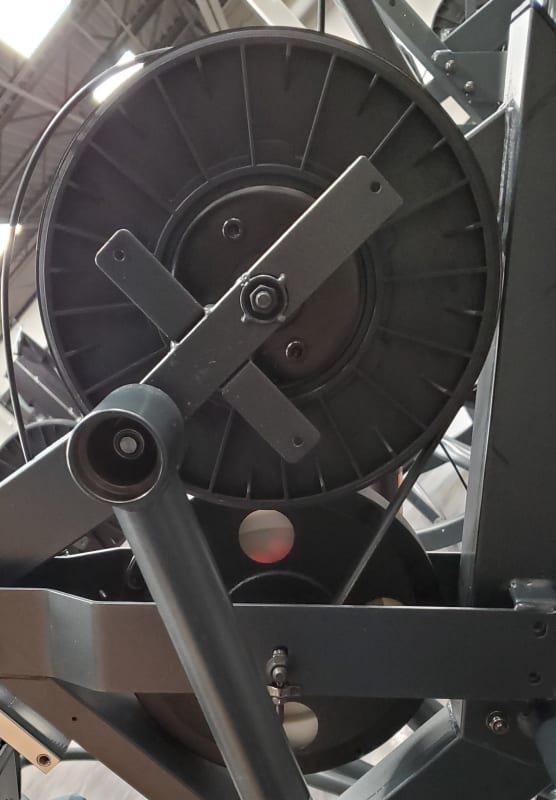
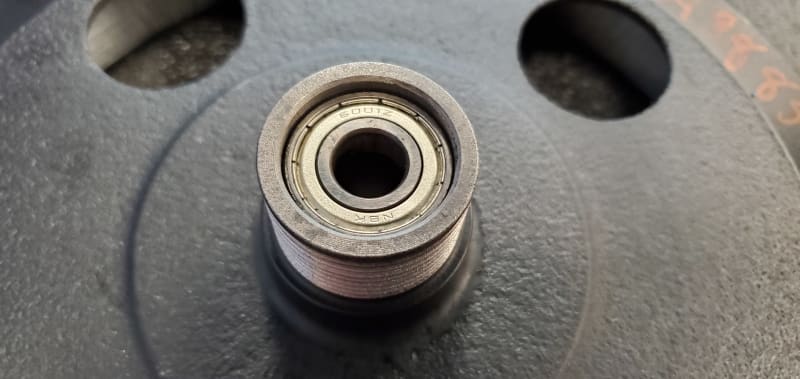
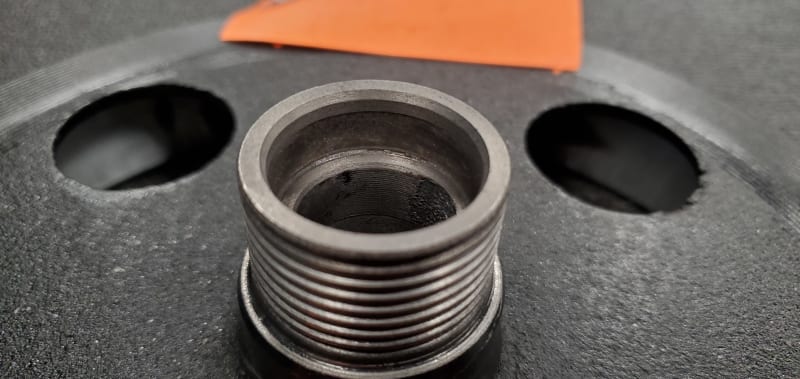
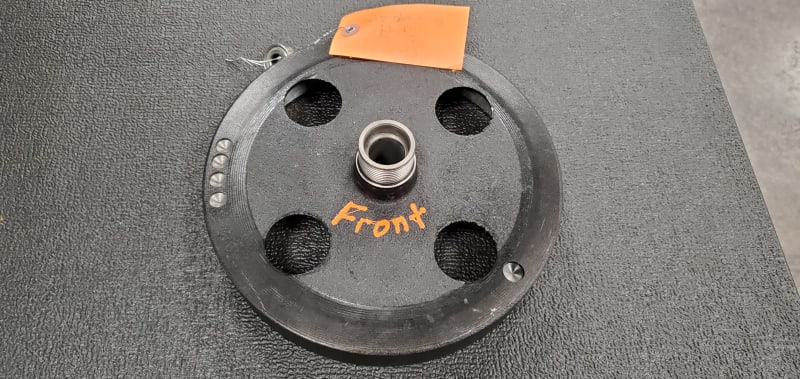
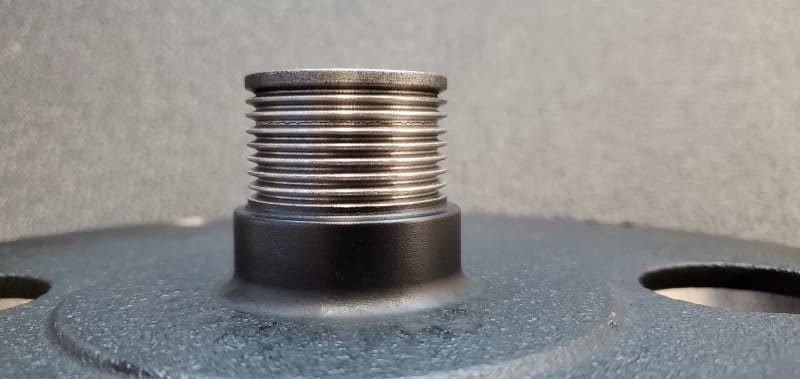