Eylon
Mechanical
- Mar 21, 2016
- 1
I need to spec a servo motor to rotate a heavy load (~1,200 lb).
The bearing surface is a round steel plate rotating on lubricated round bronze plate(6" OD).
Below are the formulas I used for the calculations.
Fn and P are the force and pressure acting on the rotating plate by the mass.
r i&o are the plate diameters. Tb is the required torque.
My questions:
1. Does anybody have experience with a similar application or calculation and can verify the formulas? The resulted torque seems very large to me.
2. Is the friction coefficient (0.2) makes sense?
Thank you.
The bearing surface is a round steel plate rotating on lubricated round bronze plate(6" OD).
Below are the formulas I used for the calculations.
Fn and P are the force and pressure acting on the rotating plate by the mass.
r i&o are the plate diameters. Tb is the required torque.
My questions:
1. Does anybody have experience with a similar application or calculation and can verify the formulas? The resulted torque seems very large to me.
2. Is the friction coefficient (0.2) makes sense?
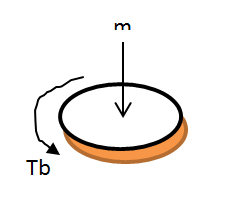
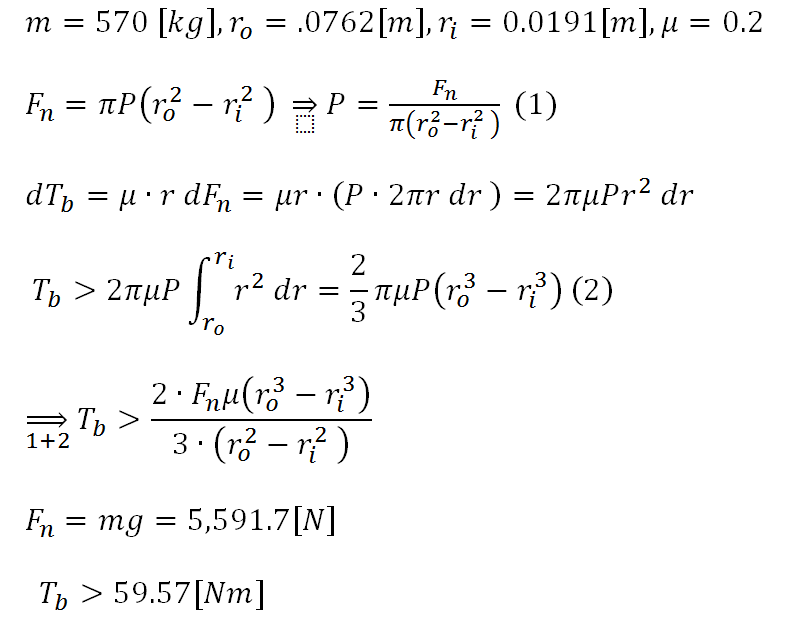
Thank you.