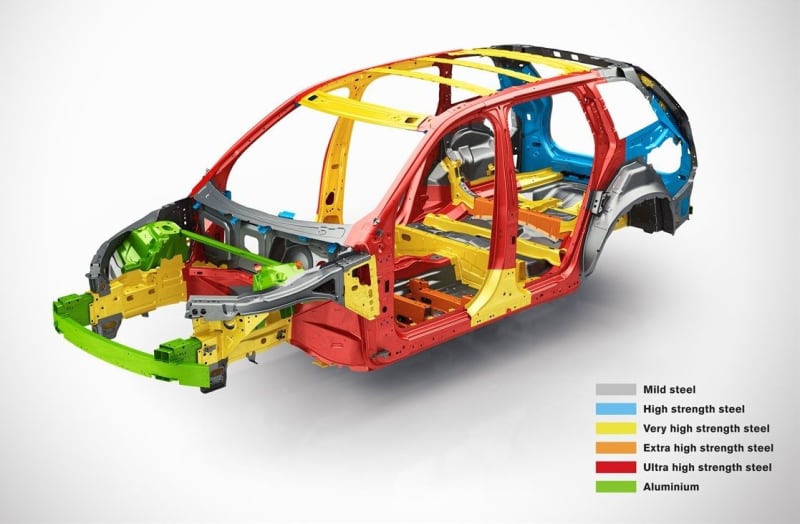
Just saw the above image on LinkedIn.
As a welding engineer, I'm wondering:
1) is it correct, that the fromt suspension turrets are in aluminium, (cast/deep drawn?)
and if so,
2) how are they connected to the steel frame (conventional welding isn't an option, that leaves deformation joining, fastening using bolts or rivets, adhesives, ...) ?
I'd say these are fairly high (cyclic) loaded parts, so aluminium seems not logical, but on the other hand I have zero experience in car frame, unibody or chassis design, so there's that if this is a stupid question...