MattEdwards
Mechanical
I have a grey part (A) with two concentric holes, that form a hinge along with a blue mating part (B) and two pins:
I want to ensure that part B will be aligned with datum Y on part A once assembled, so need an axis between the two holes in A to be perpendicular to datum Y. I can think of two ways to do this:
- Make one of the holes a datum, and align the other two it using true position
- Use a single perpendicularity tolerance attached to both holes with common zone (CZ)
Are there any other ways? Which way is best?
I'm in the UK working to ISO standards, but interested to hear standard practise for ASME too.
Cheers,
Matt
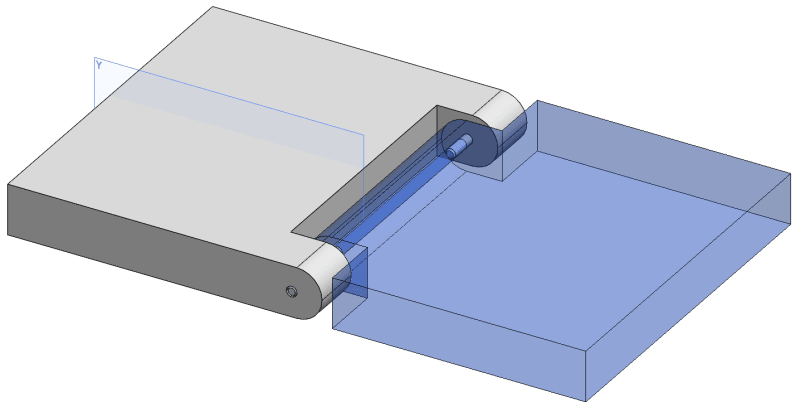
I want to ensure that part B will be aligned with datum Y on part A once assembled, so need an axis between the two holes in A to be perpendicular to datum Y. I can think of two ways to do this:
- Make one of the holes a datum, and align the other two it using true position
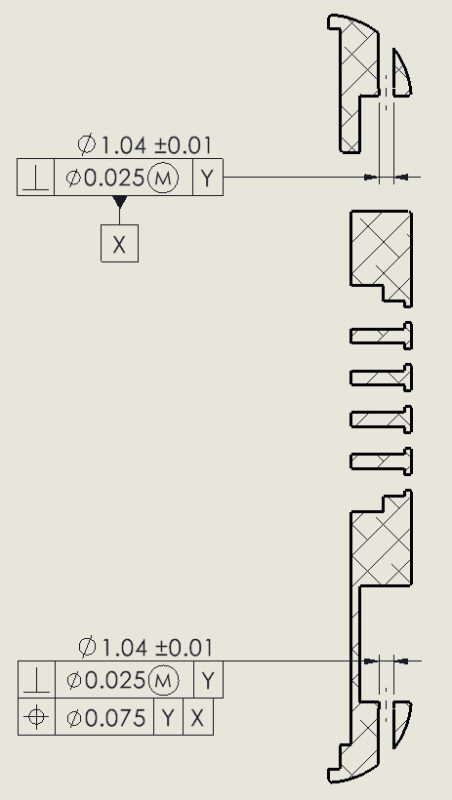
- Use a single perpendicularity tolerance attached to both holes with common zone (CZ)

Are there any other ways? Which way is best?
I'm in the UK working to ISO standards, but interested to hear standard practise for ASME too.
Cheers,
Matt