Hi,
I have this assembly where the green part is attached to the blue one, but green part can rotate around the attachment axis to the blue part. The distance from the holes on the blue part to the hole on the green is critical. Being B and C the holes on the blue part, I am wondering how I could callout the Hole on the Green part.
My concern is that if a CMM is used and they don't set the green part nominally with respect to CAD, it will show Out of Spec when in reality it could function as desired.
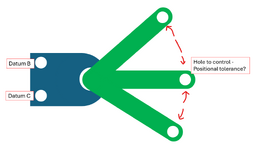
I have this assembly where the green part is attached to the blue one, but green part can rotate around the attachment axis to the blue part. The distance from the holes on the blue part to the hole on the green is critical. Being B and C the holes on the blue part, I am wondering how I could callout the Hole on the Green part.
My concern is that if a CMM is used and they don't set the green part nominally with respect to CAD, it will show Out of Spec when in reality it could function as desired.
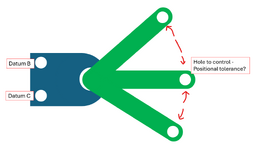