Hi,
I have started to design a lot of bent sheet metal parts. I am comfortable using GDT on machined parts or flat sheet metal parts but applying it to bent sheet metal parts can be sometimes confusing. For parts like the one below, is it easier from an inspection position to use profile tolerances to control the outer edge/surfaces or just regular plus/minus linear and angular dimensions/tolerancing. With parts that have a lot of bends it seems if you use profile tolerance with respect to your datums, they need to be large to accommodate the position and angle deviations. In the part below if you want to control the angle tighter than the position of the surface, should you use a larger profile tolerance on the surface to control position and then an angularity tolerance to refine the angle or just remove basic dimensions and use regular linear and angular tolerances? When it comes to datums, it seems hard to have just one setup as the larger profile tolerances needed could allow some of the features to interfere. What is the best way then to dimension and tolerance parts like below? Thank you for the assistance.
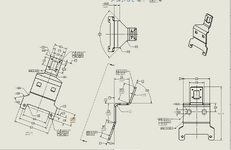
I have started to design a lot of bent sheet metal parts. I am comfortable using GDT on machined parts or flat sheet metal parts but applying it to bent sheet metal parts can be sometimes confusing. For parts like the one below, is it easier from an inspection position to use profile tolerances to control the outer edge/surfaces or just regular plus/minus linear and angular dimensions/tolerancing. With parts that have a lot of bends it seems if you use profile tolerance with respect to your datums, they need to be large to accommodate the position and angle deviations. In the part below if you want to control the angle tighter than the position of the surface, should you use a larger profile tolerance on the surface to control position and then an angularity tolerance to refine the angle or just remove basic dimensions and use regular linear and angular tolerances? When it comes to datums, it seems hard to have just one setup as the larger profile tolerances needed could allow some of the features to interfere. What is the best way then to dimension and tolerance parts like below? Thank you for the assistance.
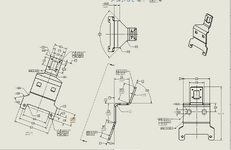
Last edited: