Okay, I know there will be a multitude of questions before anyone can give a proper answer, simply because I don't know exactly the criteria I need to stipulate when asking the following question correctly.
But basically I'm trying to get a ballpark figure of how much it would take to get a batch of gears manufactured.
I realise I won't know how to specify the gear correctly, so partly I'm hoping this thread will help me do that also.
Okay, I've attached an image that gives an idea of what the gear roughly looks like, although this is from a different engine entirely, but basically it's this type of gear. The gear will actually be splined internally also which isn't illustrated in the attached image.
I can get my hands on the real gear sample later but I don't have it just yet.
I'm just curious how cost effective it is to do this, or if it is a non-starter due to expense.
For example a price for
10 off,
50 off or
100 off
The gear is for a motorcycle gearbox which is now obsolete and can't be purchased.
I believe it is DP12 or thereabouts, to give you an idea of the scale of things.
The image attached has stub teeth whereas the actual gear I believe has a more conventional tooth form from memory.
I have no idea of the tolerances required, materials, surface finishing operation etc, so I hope someone will advice me what they need to be rather than ask me what I want them to be.
Thanks
P.S. I don't know the correct term for "undercut" drive dogs, but I mean that the engagement faces are angled a few degrees, sort of like dovetailed, to maintain engagement within the mating gear.
But basically I'm trying to get a ballpark figure of how much it would take to get a batch of gears manufactured.
I realise I won't know how to specify the gear correctly, so partly I'm hoping this thread will help me do that also.
Okay, I've attached an image that gives an idea of what the gear roughly looks like, although this is from a different engine entirely, but basically it's this type of gear. The gear will actually be splined internally also which isn't illustrated in the attached image.
I can get my hands on the real gear sample later but I don't have it just yet.
I'm just curious how cost effective it is to do this, or if it is a non-starter due to expense.
For example a price for
10 off,
50 off or
100 off
The gear is for a motorcycle gearbox which is now obsolete and can't be purchased.
I believe it is DP12 or thereabouts, to give you an idea of the scale of things.
The image attached has stub teeth whereas the actual gear I believe has a more conventional tooth form from memory.
I have no idea of the tolerances required, materials, surface finishing operation etc, so I hope someone will advice me what they need to be rather than ask me what I want them to be.
Thanks
P.S. I don't know the correct term for "undercut" drive dogs, but I mean that the engagement faces are angled a few degrees, sort of like dovetailed, to maintain engagement within the mating gear.
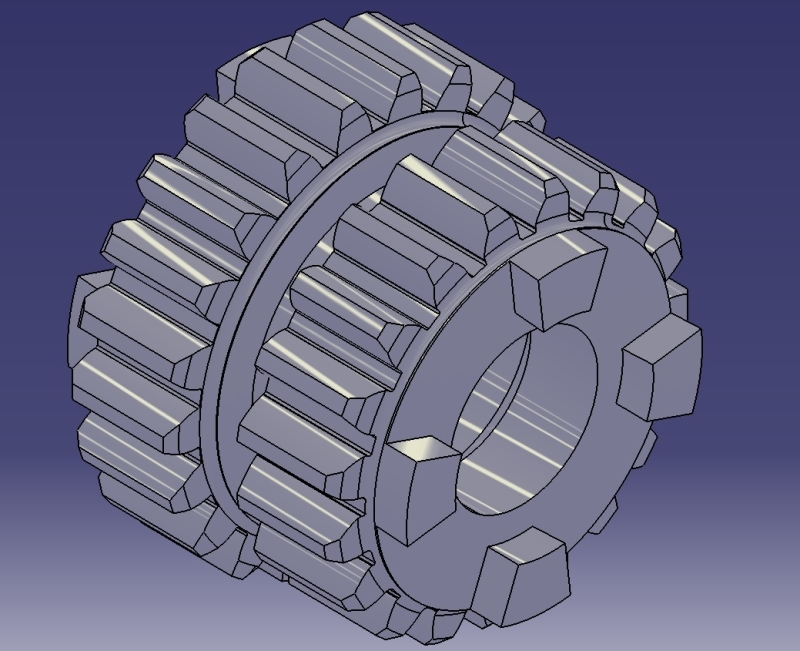