I need some suggestions on how to model an assembly.
I have simplified what I am modeling in the picture below. There is a Hexagonal shaft placed into a female hexagonal base. There is a small amount of clearance between the two parts radially speaking(no initial radial contact). The shafft end contacts the bottom o the base. Let's assume there is a small screw or spring holding the base to the end of the shaft.
Initial conditions..the base is fully fixed and there is a small torque on the shaft's main axis and also a load applied normal to the highlighted surface.
How can I generate the FE model. I used the contact constraint, but my assembly has no constraints which limit rotation of the parts because there is the clearance between the two. In actuality, there will be contact between the hexagonal surfaces, once loads are applied. Also, I thought about using the spring connection between the base and the shaft to help keep the parts together. I have gotten results some results, but I am not 100% confident in the FE model.
Any tips on the assembly or what type of conenctions to use would be appreciated. Thanks!
I have simplified what I am modeling in the picture below. There is a Hexagonal shaft placed into a female hexagonal base. There is a small amount of clearance between the two parts radially speaking(no initial radial contact). The shafft end contacts the bottom o the base. Let's assume there is a small screw or spring holding the base to the end of the shaft.
Initial conditions..the base is fully fixed and there is a small torque on the shaft's main axis and also a load applied normal to the highlighted surface.
How can I generate the FE model. I used the contact constraint, but my assembly has no constraints which limit rotation of the parts because there is the clearance between the two. In actuality, there will be contact between the hexagonal surfaces, once loads are applied. Also, I thought about using the spring connection between the base and the shaft to help keep the parts together. I have gotten results some results, but I am not 100% confident in the FE model.
Any tips on the assembly or what type of conenctions to use would be appreciated. Thanks!
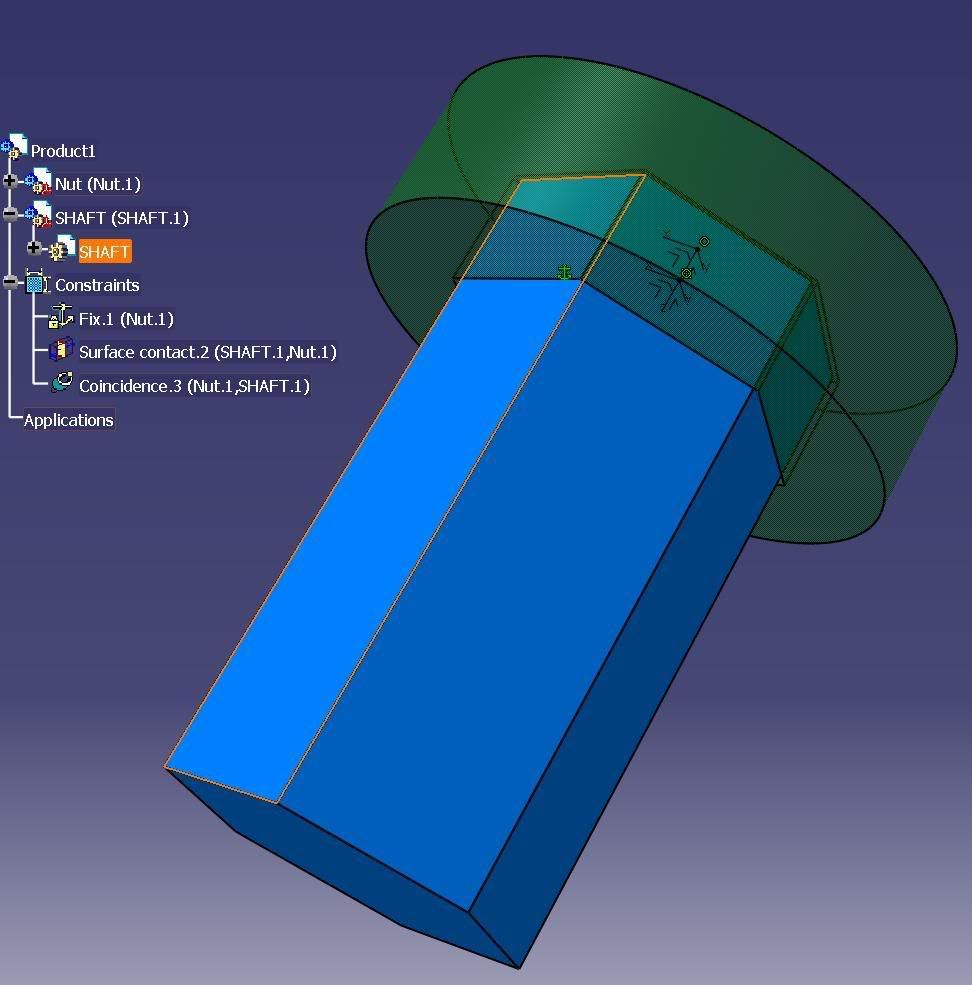