Hello,
I am conducting a static analysis in which I have both glue and touch contacts.
My problem is to know how to actually define multiple contacts, and within it, the BCPARA entry where I define the LINCNT
paramater to 1 for the glue contact, but I cannot define another BCPARA card with LINCNT = 0 for the
touch contact. I read in the QRG that only one BCPARA card is admitted in the SOL 101 and that it must have ID = 0.
So, my problem is how to define many different contacts in the same analysis.
The first contact I did was the glue contact and it worked, and now I am adding the touch contact.
One additional question concerning the glued contacts is : Is it normal to not obtain contact outputs when working with glued contacts?
Because I have no outputs, even if I put as global output BOUTPUT = ALL.
Furthermore, when I run the analysis, it does not converge. And the .f06 file gives me this message :
*** USER WARNING MESSAGE 8156 (MCN1GCK)
GENERAL CONTACT JOB WITH THE GLUE OPTION WILL BE ACTIVATED INSTEAD OF PERMANENT GLUE.
NLGLUE IN BCPARA (ID=0) WILL BE SET TO 1.
User Information: The model has both of glue and non-glue contact definitions.
SOL101 and SOL400 support the mixed glued contact and the permanent glue contact changes to the mixed glue contact.
I will leave and image of the model :
The glue contact is for the link between the cradles and the base plate, whereas the touch contact is for the cradles/tank contact.
I will also leave attached the .bdf file (in a .zip file given that it has more than 20mb).
Thanks in advance !
Cordially,
EC
I am conducting a static analysis in which I have both glue and touch contacts.
My problem is to know how to actually define multiple contacts, and within it, the BCPARA entry where I define the LINCNT
paramater to 1 for the glue contact, but I cannot define another BCPARA card with LINCNT = 0 for the
touch contact. I read in the QRG that only one BCPARA card is admitted in the SOL 101 and that it must have ID = 0.
So, my problem is how to define many different contacts in the same analysis.
The first contact I did was the glue contact and it worked, and now I am adding the touch contact.
One additional question concerning the glued contacts is : Is it normal to not obtain contact outputs when working with glued contacts?
Because I have no outputs, even if I put as global output BOUTPUT = ALL.
Furthermore, when I run the analysis, it does not converge. And the .f06 file gives me this message :
*** USER WARNING MESSAGE 8156 (MCN1GCK)
GENERAL CONTACT JOB WITH THE GLUE OPTION WILL BE ACTIVATED INSTEAD OF PERMANENT GLUE.
NLGLUE IN BCPARA (ID=0) WILL BE SET TO 1.
User Information: The model has both of glue and non-glue contact definitions.
SOL101 and SOL400 support the mixed glued contact and the permanent glue contact changes to the mixed glue contact.
I will leave and image of the model :
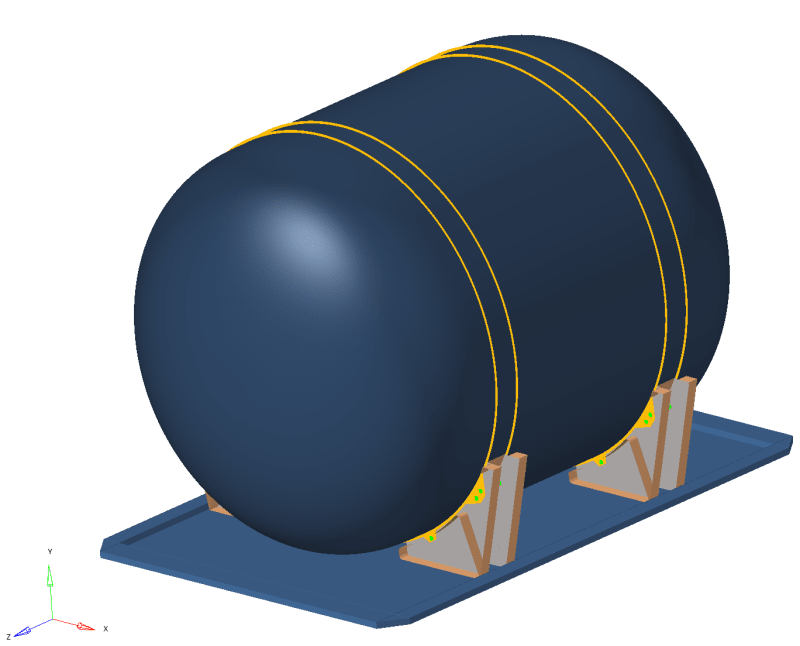
The glue contact is for the link between the cradles and the base plate, whereas the touch contact is for the cradles/tank contact.
I will also leave attached the .bdf file (in a .zip file given that it has more than 20mb).
Thanks in advance !
Cordially,
EC