CivilEngineerUK
Civil/Environmental
I have a steel column welded on a base plate, size 500x400x30mm. Anchors are M48, which are preloaded. The steel column is connected to a concrete pile.
1) Which grout thickness should be used?
2) Dynamic/fatigue load occur in the connection (preloading anchors are used). Working life is 120 years. Which type of grout should be used, epoxy og cementitious grout?
3) What is the best way to make the 45 degree slope of the grout?
1) Which grout thickness should be used?
2) Dynamic/fatigue load occur in the connection (preloading anchors are used). Working life is 120 years. Which type of grout should be used, epoxy og cementitious grout?
3) What is the best way to make the 45 degree slope of the grout?
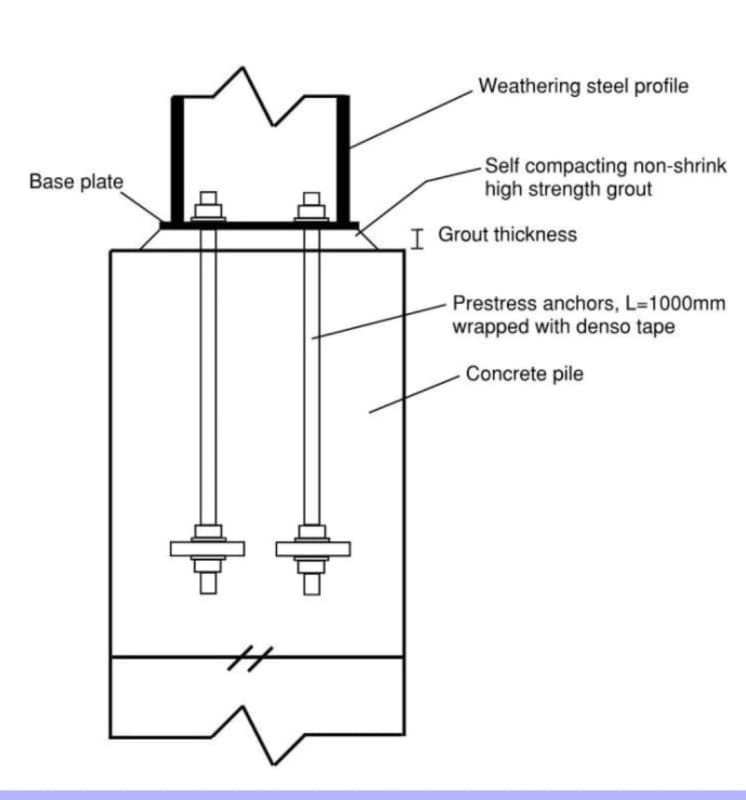