Last night I got called to a slicer machine with about 20 knife blades.
The complaint was it kept stopping randomly with the random running from a minute to about 6 months.
Luckily it had dropped during the day down to staying off.
It was thought that the control cabinet was too hot as it was pretty roasty hot so filtered air was fanned thru it. That seemed to work for many months before it was back. They'd taken to opening the cabinet up, which required the disconnect to be opened, and then they'd push the RESET button on the unpowered VFD, close it back up and it would run for a while before checking-out again.
Turned out one of the wires from the operator panel speed control pot where it entered the VFD control terminal block had broken every (probably) non-annealed strand of its crappy wire except ONE. That one was the center strand in cage-clamp bunch of broken wires. This allowed temperature shifts, vibration, machine bumps, VFD Reset button presses, hell, probably moth farts, to connect and disconnect the speed signal.
Anyway here's my question:
This disconnect would feed the VFD a 0.0 speed command and it would decelerate down to stopped looking stopped! Of course workers might do something thinking the system was "stopped" but a bump would suddenly feed it a 57.7Hz signal and it would take off!
Got any ideas how to prevent this behavior? Something that could see the speed signal and would actually put the VFD into stop or ??.
Keith Cress
kcress -
The complaint was it kept stopping randomly with the random running from a minute to about 6 months.
Luckily it had dropped during the day down to staying off.
It was thought that the control cabinet was too hot as it was pretty roasty hot so filtered air was fanned thru it. That seemed to work for many months before it was back. They'd taken to opening the cabinet up, which required the disconnect to be opened, and then they'd push the RESET button on the unpowered VFD, close it back up and it would run for a while before checking-out again.
Turned out one of the wires from the operator panel speed control pot where it entered the VFD control terminal block had broken every (probably) non-annealed strand of its crappy wire except ONE. That one was the center strand in cage-clamp bunch of broken wires. This allowed temperature shifts, vibration, machine bumps, VFD Reset button presses, hell, probably moth farts, to connect and disconnect the speed signal.
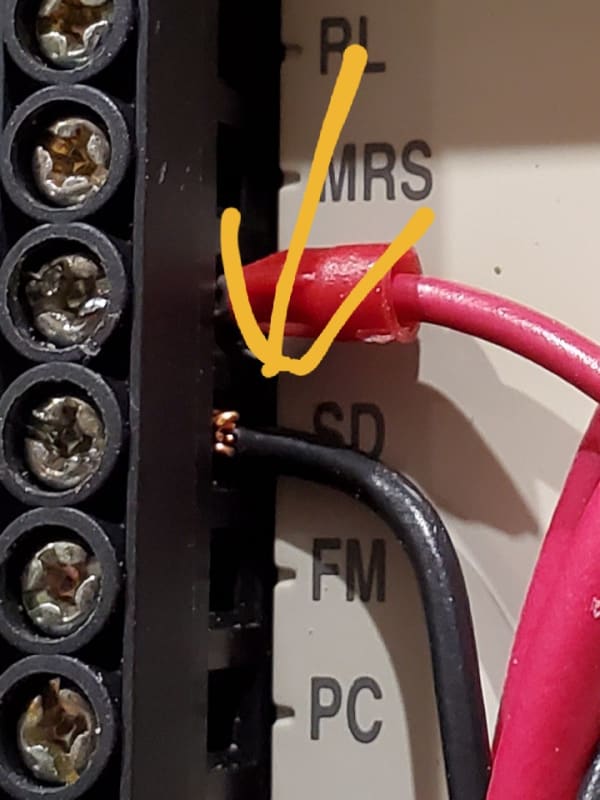
Anyway here's my question:
This disconnect would feed the VFD a 0.0 speed command and it would decelerate down to stopped looking stopped! Of course workers might do something thinking the system was "stopped" but a bump would suddenly feed it a 57.7Hz signal and it would take off!
Got any ideas how to prevent this behavior? Something that could see the speed signal and would actually put the VFD into stop or ??.
Keith Cress
kcress -