See an example, two cooling tower, two identical pump parallel, 1350 gpm each required for one CT to run one chiller. During the head calculation, I consider one pump throughout 1350 gpm? One veteran told me that put the 2700 gpm from header. Is it true, because I want to calculate the head for only one pump; throughout year, one pump will only work out.
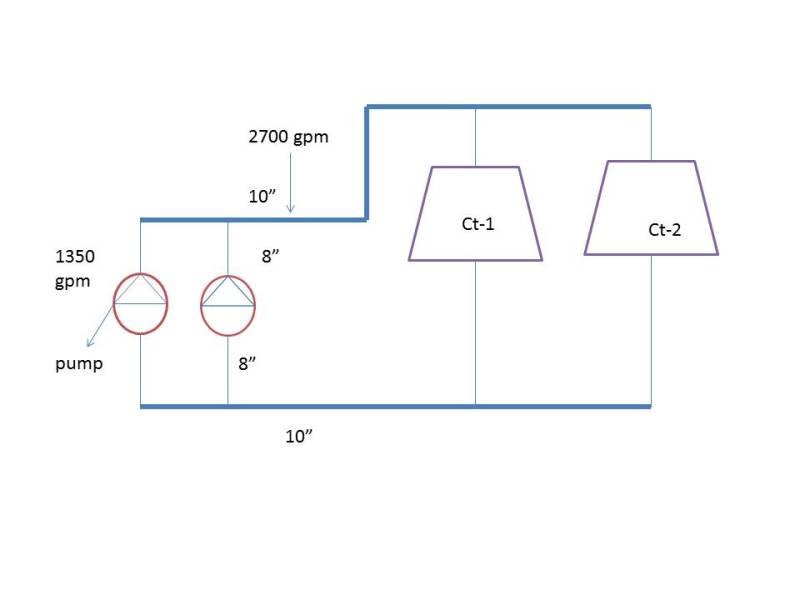