I'm working on a project where the contract plans have temporary steel jacking/erection towers that are supported on new concrete footings around existing concrete columns. The contract shows the steel base plates resting directly on the new concrete.
The contractor is proposing to using leveling nuts and a grout bed underneath the base plates.
Normally, I probably wouldn't give this a second thought, but the columns are supporting significant vertical loads (LL ~ 340 kips, DL ~ 170 kips) and will probably be in place for 3-4 months.
Is there any history or reason for concern with a heavily loaded column crushing the unconfined grout bed and overloading the leveling nuts? Other thoughts?
Thanks for any input!
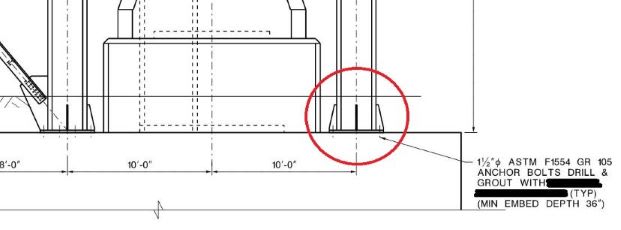
The contractor is proposing to using leveling nuts and a grout bed underneath the base plates.
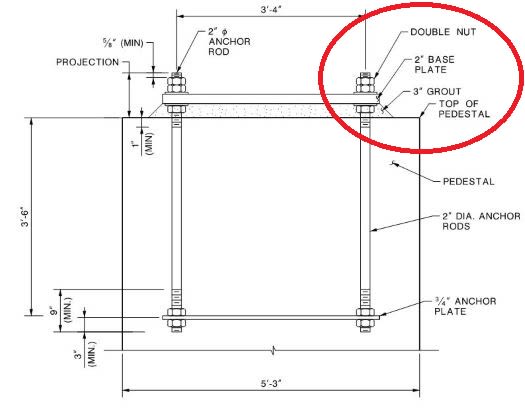
Normally, I probably wouldn't give this a second thought, but the columns are supporting significant vertical loads (LL ~ 340 kips, DL ~ 170 kips) and will probably be in place for 3-4 months.
Is there any history or reason for concern with a heavily loaded column crushing the unconfined grout bed and overloading the leveling nuts? Other thoughts?
Thanks for any input!