SMKRe
Mechanical
- May 17, 2023
- 44
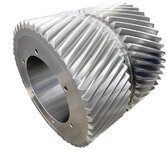
reference image used in the static structural analysis. I have carried out analysis in ANSYS for calculating the gear tooth deformation for various pitch line velocities. gear tooth is expanded/ deformed as shown below. Why the gear tooth is not having the same deformation across the face width due to centrifugal force (because of high rotational speeds)?
could any body tell why the deformation is more at center and compared to end of the teeth.
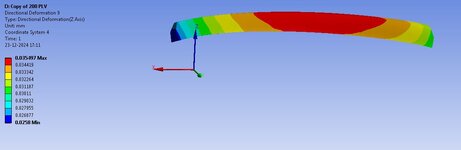
along the gear tooth face width face width the deformation is maximum the outside, no deformation at around 1/3 from inside and again deformation