Consider this setup of a boiler:
red is hot water/flow, blue is cold/return. The boiler is non-modulating. This is an existing plant with no real documentation for the heating system. Tehre will be numerous refurbishment works, part of this is a new PLC for the heating system that I may write the narrative for.
Things I forgot in my little drawing: a TC on the suction side of the pump, position encoder on the three-way valve
1. The way I understand it is this:
If the temeprature in the return is too cold, the three-way valve will mix hot water into the return flow.
The flow through the boiler is determined by the pump & constant, so at constant power the temp. rise between return and flow will be constant. So if I keep the return temp. constant I will get my constant, desired flow temp.
The only way to implement this control scheme is a sort of table where for a range of return-temps I have a setting for the valve.
Question 1: Is my understanding correct?
2. Modulating burner
There's two of these boilers, one will be swapped for a modulating burner. The two will never be active a t the same time.
Question 2: Is there any reason to keep the three-way valve and control scheme, and not just have pump run and adjust the burner power to temp. in flow (?
red is hot water/flow, blue is cold/return. The boiler is non-modulating. This is an existing plant with no real documentation for the heating system. Tehre will be numerous refurbishment works, part of this is a new PLC for the heating system that I may write the narrative for.
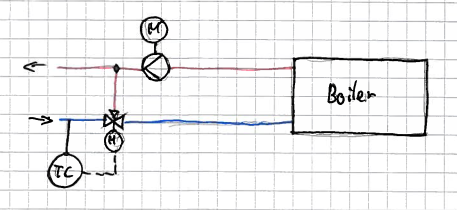
Things I forgot in my little drawing: a TC on the suction side of the pump, position encoder on the three-way valve
1. The way I understand it is this:
If the temeprature in the return is too cold, the three-way valve will mix hot water into the return flow.
The flow through the boiler is determined by the pump & constant, so at constant power the temp. rise between return and flow will be constant. So if I keep the return temp. constant I will get my constant, desired flow temp.
The only way to implement this control scheme is a sort of table where for a range of return-temps I have a setting for the valve.
Question 1: Is my understanding correct?
2. Modulating burner
There's two of these boilers, one will be swapped for a modulating burner. The two will never be active a t the same time.
Question 2: Is there any reason to keep the three-way valve and control scheme, and not just have pump run and adjust the burner power to temp. in flow (?