itskylecook
Aerospace
Good afternoon,
I am running into an issue when installing HL12VAP5 Pins with HL1087ATW5 Collars of varying grip lengths but generally between 3's and 5's. When torqueing the Collar there are instances (at least 20%) where the Pin will shear off at the point where the allen key is engaged. We install 100s of Size 5 Hi-Loks per day and 1000s per build so a minimum of 20% failed installs is a pretty significant number.
After searching through the forum I came across a thread where Will Taylor (WKTaylor) stated "An 'integral-washer-collar' will likely induce a significantly higher torque-tension for 'same torque' relative-to a 'plain' collar [due to lower torque-turning friction]." I am under the impression that this is the root cause however I am not sure what the most effective and practical way would be to address it. I also believe that Size 5 Hi-Loks must be an unlucky thickness because we do not have any issues with Size 6 Hi-Loks and greater.
We tested how much torque is being applied to the Collar when the Pin shears off and there were instances when it occurred at 30 in-lb which is the minimum for a HL1087A Collar. We also applied additional lubricant to the Pin and Collar to no effect. Additionally, we used a Plain HL1087A-5 Collar with a .016" thick aluminum washer to simulate the HL1087ATW5 and all Hi-Loks were installed successfully.
Our current solution is to increase the grip length by (1) and install a .032" thick aluminum washer under the HL1087AWT5 Collar in order to move the Collar closer to the solid shank part of the Pin. We successfully install Hi-Loks in this configuration however I am wondering if there is a better solution instead of a reactive approach to the Pins shearing off. As of right now, the only option I can think of is to install HL1087A-5 Collars with .016" aluminum washers in place of HL1087ATW5 Collars as a proactive way to avoid sheared Pins.
Any help or inside would be greatly appreciated,
Kyle
I am running into an issue when installing HL12VAP5 Pins with HL1087ATW5 Collars of varying grip lengths but generally between 3's and 5's. When torqueing the Collar there are instances (at least 20%) where the Pin will shear off at the point where the allen key is engaged. We install 100s of Size 5 Hi-Loks per day and 1000s per build so a minimum of 20% failed installs is a pretty significant number.
After searching through the forum I came across a thread where Will Taylor (WKTaylor) stated "An 'integral-washer-collar' will likely induce a significantly higher torque-tension for 'same torque' relative-to a 'plain' collar [due to lower torque-turning friction]." I am under the impression that this is the root cause however I am not sure what the most effective and practical way would be to address it. I also believe that Size 5 Hi-Loks must be an unlucky thickness because we do not have any issues with Size 6 Hi-Loks and greater.
We tested how much torque is being applied to the Collar when the Pin shears off and there were instances when it occurred at 30 in-lb which is the minimum for a HL1087A Collar. We also applied additional lubricant to the Pin and Collar to no effect. Additionally, we used a Plain HL1087A-5 Collar with a .016" thick aluminum washer to simulate the HL1087ATW5 and all Hi-Loks were installed successfully.
Our current solution is to increase the grip length by (1) and install a .032" thick aluminum washer under the HL1087AWT5 Collar in order to move the Collar closer to the solid shank part of the Pin. We successfully install Hi-Loks in this configuration however I am wondering if there is a better solution instead of a reactive approach to the Pins shearing off. As of right now, the only option I can think of is to install HL1087A-5 Collars with .016" aluminum washers in place of HL1087ATW5 Collars as a proactive way to avoid sheared Pins.
Any help or inside would be greatly appreciated,
Kyle
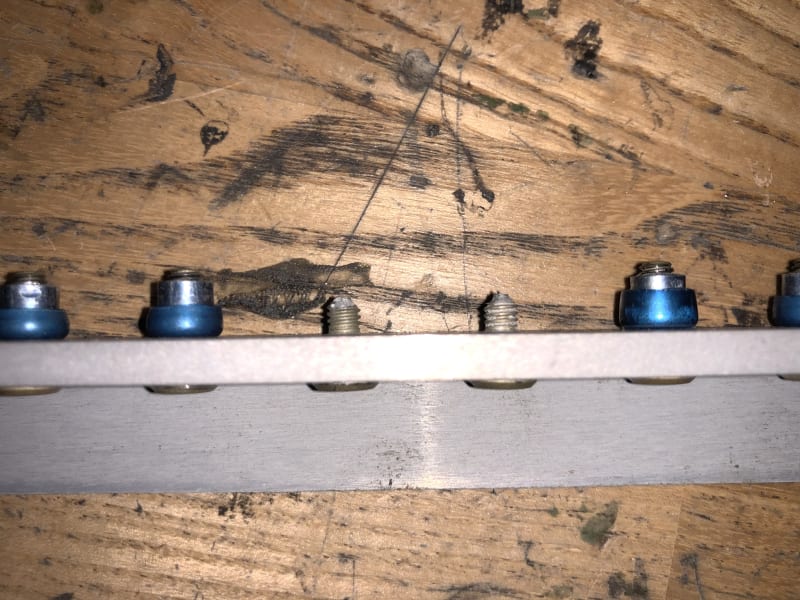
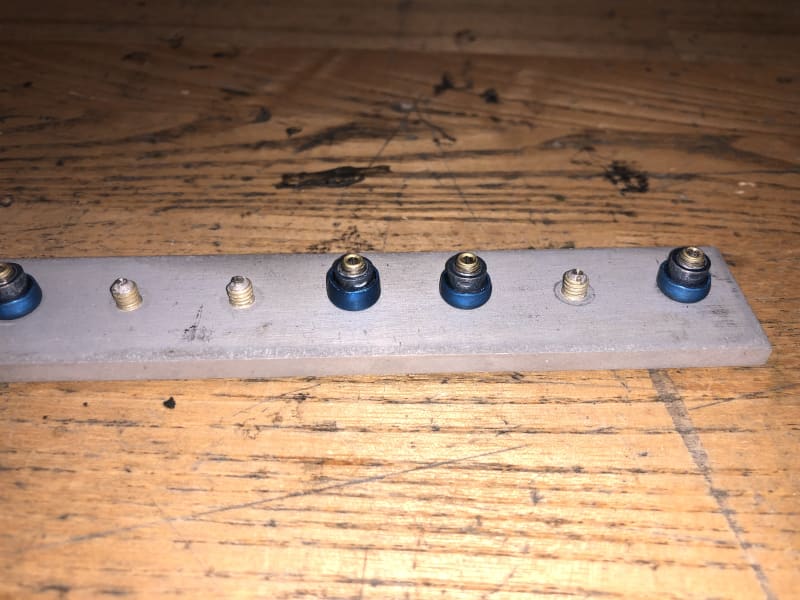
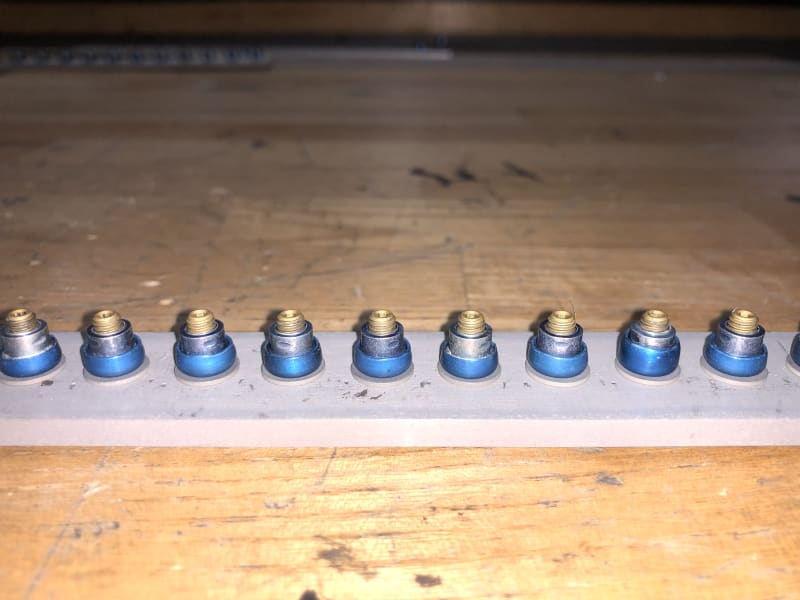
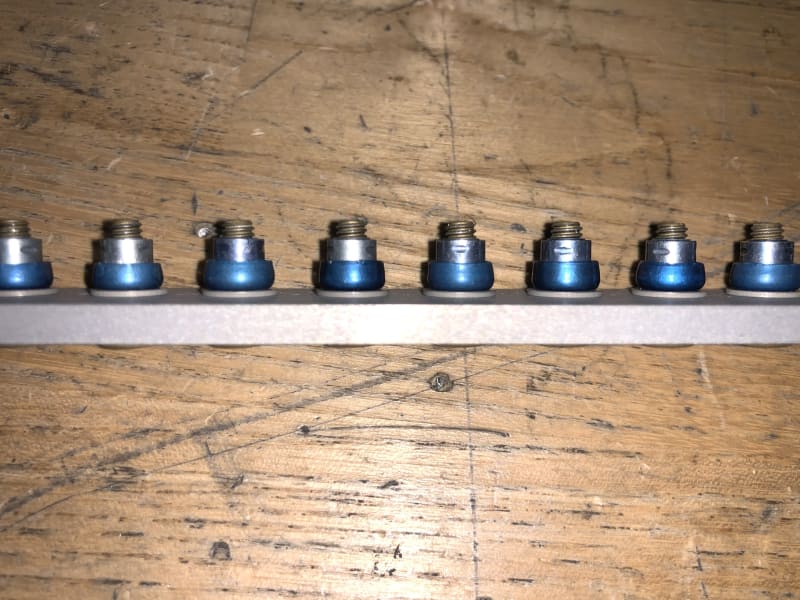