I am modeling a cantilever beam to carry a weight with a support (black line).
I want to check the impact of modeling the hinge at the end... if I use MPC element to allow rotation, I can almost two times deflection downwards from frictional contact at the hinge.
I understand in reality, there is a tight gap between the pin and hole... and the touching area should be at the top... which approach is more reality? Thank you!
I want to check the impact of modeling the hinge at the end... if I use MPC element to allow rotation, I can almost two times deflection downwards from frictional contact at the hinge.
I understand in reality, there is a tight gap between the pin and hole... and the touching area should be at the top... which approach is more reality? Thank you!
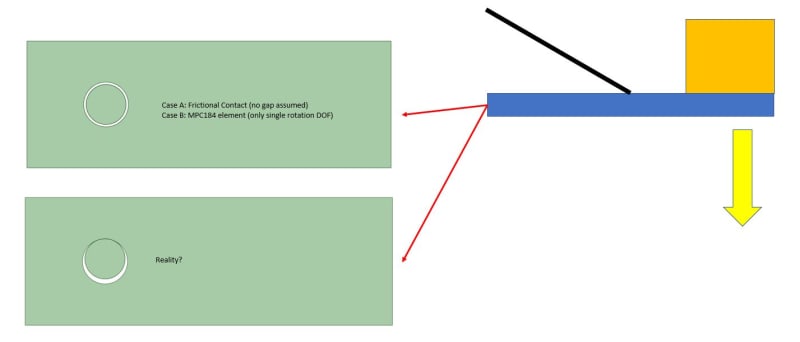