Hey
I am designing a connection of cantilever beam with end plate connected to HSS Beam. The customer doesn't want to weld the end plate to the beam so I proposed the HSS expansion bolts
it seems that these bolts are very expensive so they came back to me asking for different type of connection. Is there any other option that I don't know ?
Ultimate tensile load / bolt = 4400 lbs
Ultimate Shear / bolt = 390 lbs
I am designing a connection of cantilever beam with end plate connected to HSS Beam. The customer doesn't want to weld the end plate to the beam so I proposed the HSS expansion bolts
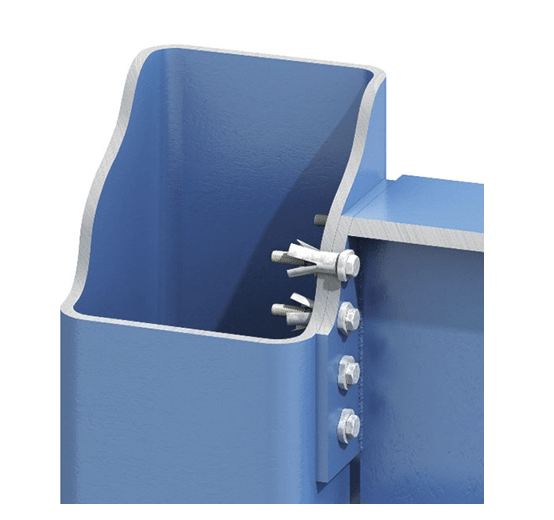
it seems that these bolts are very expensive so they came back to me asking for different type of connection. Is there any other option that I don't know ?
Ultimate tensile load / bolt = 4400 lbs
Ultimate Shear / bolt = 390 lbs