Hello,
I was sourcing some quick links for an application the other day and out of curiosity started thinking about how these are manufactured. I have not come up with a method so I thought I would ask here.
The requirements for the threads seem to be:
1. Aligned axially so the "gate" (glorified standoff) can move back and forth
2. Timed properly so the gate can thread on and off to close the link while still threaded on the other side
From what I can tell, there may be some swage marks where a die closes around the link to upset a stop shoulder and form threads. That would have to be done before the nut is threaded on. Also, how is the link formed with the nut in place when there is not a lot of room from the nut to the bend radius?
For reference, here is a picture of what I'm referring to:
Any thoughts on how these are made?
Thanks,
Kyle
I was sourcing some quick links for an application the other day and out of curiosity started thinking about how these are manufactured. I have not come up with a method so I thought I would ask here.
The requirements for the threads seem to be:
1. Aligned axially so the "gate" (glorified standoff) can move back and forth
2. Timed properly so the gate can thread on and off to close the link while still threaded on the other side
From what I can tell, there may be some swage marks where a die closes around the link to upset a stop shoulder and form threads. That would have to be done before the nut is threaded on. Also, how is the link formed with the nut in place when there is not a lot of room from the nut to the bend radius?
For reference, here is a picture of what I'm referring to:
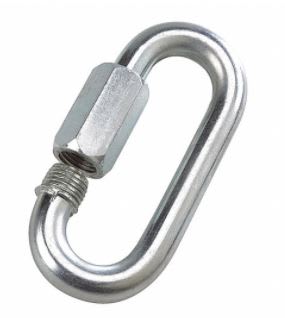
Any thoughts on how these are made?
Thanks,
Kyle