Dear valve experts,
Need some insight on how to determine (or best approach) which (Ball) valves still designed without Anti-Blow-Out stem feature.
Find below case in one of my old Plant. Fortunately no one was hurt when the lever fell of
Understand that standard wise (BS 5351 and ISO 7121) start to officially regulate the anti blow out stem design in 1986. However prior that year, the two types (with and without Anti blow out) were exist.
Question from my maintenance team: How do we know which one is which.
PS: dismantle similar valve. Find out that one had ABO stem and one didn't.
Any idea on how to approach this case gentlemen? No data on the system (SAP) and replacement of the whole corroded Ball valves (assuming its old) would hardly ever accepted based on suspicion only.
Thank you beforehand for the input.
Regards,
MR
All valves will last for years, except the ones that were poorly manufactured; are still wrongly operated and or were wrongly selected
Need some insight on how to determine (or best approach) which (Ball) valves still designed without Anti-Blow-Out stem feature.
Find below case in one of my old Plant. Fortunately no one was hurt when the lever fell of
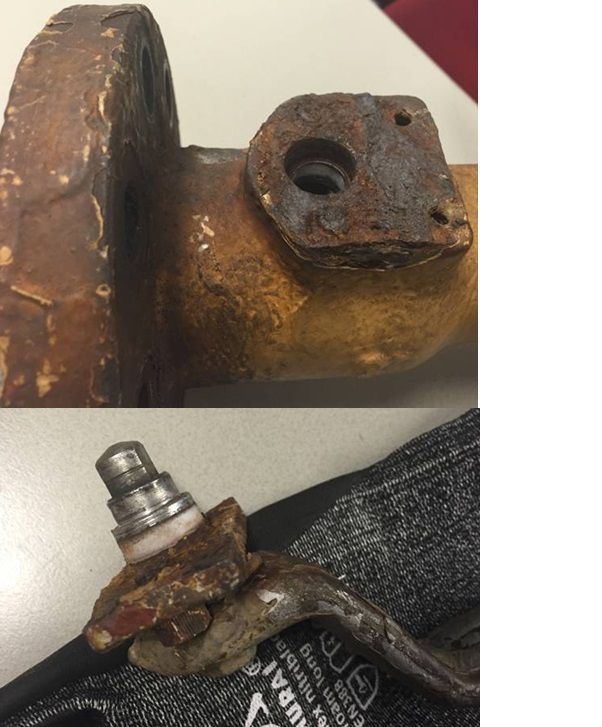
Understand that standard wise (BS 5351 and ISO 7121) start to officially regulate the anti blow out stem design in 1986. However prior that year, the two types (with and without Anti blow out) were exist.
Question from my maintenance team: How do we know which one is which.
PS: dismantle similar valve. Find out that one had ABO stem and one didn't.
Any idea on how to approach this case gentlemen? No data on the system (SAP) and replacement of the whole corroded Ball valves (assuming its old) would hardly ever accepted based on suspicion only.
Thank you beforehand for the input.
Regards,
MR
All valves will last for years, except the ones that were poorly manufactured; are still wrongly operated and or were wrongly selected